|
6.2. Własności Reologiczne ciekłych substancji smarnych
6.2.1. Ciecze newtonowskie i nienewtonowskie
Zasadniczą różnicą pomiędzy trzema podstawowymi stanami skupienia materii: gazowym, ciekłym i stałym są wzajemne odległości między cząsteczkami, określające wartość sił spójności (kohezji).
W cieczach odległości międzycząsteczkowe są małe. Cząsteczki podlegają znacznym siłom przyciągania i mogą swobodnie przesuwać się względem siebie. Przemieszczanie poszczególnych cząstek lub warstw cząstek ciała względem siebie napotyka na opór sił spójności. Im większe siły spójności, tym większe są opory tarcia wewnętrznego ciała (rys. 6.5).
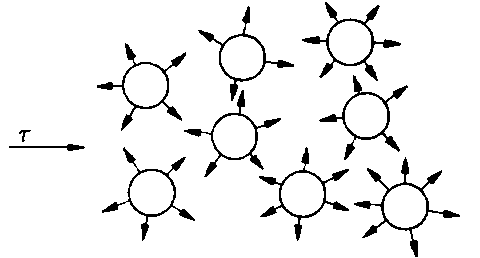
Rys. 6.5. Oddziaływanie międzycząsteczkowe w cieczy powodujące opory tarcia |
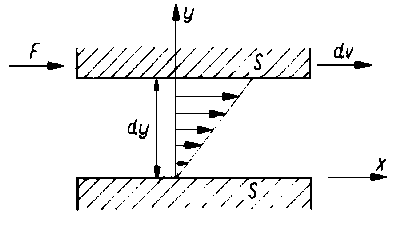
Rys. 6.6. Ruch cieczy między dwiema płytkami
|
Przepływ można określić jako proces ścinania cieczy. Jeżeli odkształcenie spowodowane przez ścinanie oznaczymy przez g, to prędkość ścinania
gdzie t = czas w s.
Prędkość ścinania charakteryzująca powstawanie odkształceń w czasie jest funkcją naprężenia stycznego t
Jest to najogólniejsze równanie reologiczne¹.
Na rys. 6.6 przedstawiono warstewkę cieczy znajdującą się między dwiema równoległymi płytkami o powierzchni S. Dolna płytka jest nieruchoma, natomiast górna może się przesuwać względem płytki dolnej. Do niej przykładamy stycznie siłę F powodującą ruch cieczy. Naprężenie ścinające t wywołujące ruch cieczy jest określone wzorem
Jeżeli naprężenie ścinające t jest proporcjonalne do gradientu prędkości cieczy, wówczas ogólne równanie reologiczne przybiera postać równania Newtona
|
t = h |
d v d y |
lub F = h S |
d v d y
| (6.5)
|
¹ Reologia jest nauką o płynięciu i deformacji wszystkich form materii pod wpływem naprężeń.
Współczynnik proporcjonalności h jest nazywany dynamiczną lepkością newtonowską. Liczbowo jest on równy sile stycznej działającej na jednostkę powierzchni warstewek cieczy, które znajdują się w jednostkowej od siebie odległości i poruszają się względem siebie z prędkością różniącą się o jednostkę. Współczynnik h wtedy jest równy jedności, gdy siła jednego niutona przypadająca na l m² powierzchni cieczy spowoduje różnice prędkości l m/s między dwiema warstewkami cieczy odległymi od siebie o l m.
Ciecze stosujące się do równania Newtona są nazywane cieczami newtonowskimi. Prędkość ścinania vśc w cieczach newtonowskich jest równoznaczna z gradientem prędkości warstewki cieczy
a więc charakteryzuje rozkład prędkości w warstwie cieczy. Dla cieczy newtonowskiej lepkość jest tylko funkcją temperatury i ciśnienia, a nie zależy od prędkości ścinania.
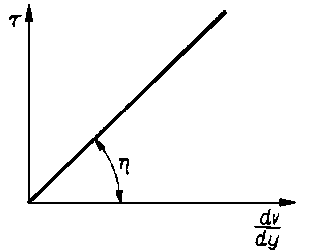
Rys. 6.7. Krzywe płynięcia cieczy newtonowskich; |
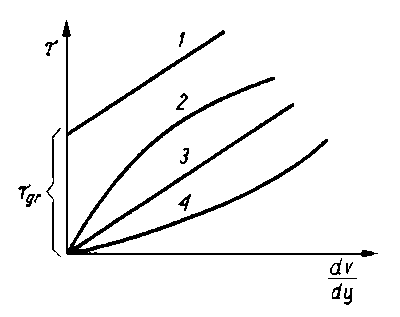
Rys. 6.8. Linia płynięcia cieczy nienewtonowskiej
- - ciecz binghamowska,
- - ciecz pseudoplastyczna,
- - ciecz newtonowska,
- - ciecz dylatacyjna
|
Krzywą płynięcia cieczy newtonowskiej jest linia prosta (rys. 6.7). Ciecze o małej i średniej masie cząsteczkowej oraz roztwory substancji o małej masie cząsteczkowej są cieczami newtonowskimi.
|
|
Ciecze nienewtonowskie są to ciecze, których krzywe płynięcia nie są liniami prostymi. Ich lepkość często jest nazywana lepkością pozorną lub strukturalną.
Przedstawiony podział cieczy na newtonowskie i nienewtonowskie ma charakter umowny, gdyż każda ciecz newtonowska zachowuje się w określonych warunkach (temperatury, ciśnienia, prędkości ścinania itp.) jak ciecz nienewtonowska.
Ciecze nienewtonowskie można podzielić na trzy zasadnicze grupy (tabl. 6.1):
- ciecze, których własności reologiczne nie zmieniają się w czasie (prędkość ścinania jest funkcją naprężenia ścinającego; charakter krzywych płynięcia tej grupy cieczy przedstawiono na rys. 6.8);
- ciecze, których własności reologiczne zmieniają się w czasie (prędkość ścinania jest funkcją naprężenia ścinającego i czasu);
- ciecze lepkosprężyste, wykazujące oprócz własności lepkościowych i efekty sprężyste.
Ciecz binghamowska (ciecz Binghama, ciecz plastyczna) - ciecz, która zaczyna płynąć dopiero wówczas, gdy naprężenie styczne t między dwiema warstewkami cieczy przekroczy pewną wartość graniczną tgr.
Przykładem takiej cieczy mogą być różnego rodzaju pasty, zawiesiny itp. Po przekroczeniu tgr struktura wewnętrzna ulega zniszczeniu i ciecz zachowuje się jak ciecz newtonowska. Z chwilą gdy naprężenie styczne zmniejszy się poniżej tgr to struktura wewnętrzna zostaje odbudowana.
Ciecz pseudoplastyczna - nie ma granicy płynięcia, lepkość pozorna maleje ze wzrostem prędkości ścinania. Ciecze takie mają zazwyczaj niesymetrycznie zbudowane cząstki (np. o wydłużonym kształcie liniowym). W miarę zwiększania prędkości ścinania cząstki te przyjmują uporządkowane ułożenie, wskutek czego zmniejszają się opory tarcia, a więc i lepkość pozorna.
Ciecz dylatacyjna - nie ma granicy płynności. Lepkość pozorna rośnie w miarę wzrostu prędkości ścinania (przykładem może być mokry piasek).
Podczas szybkiego ścinania zawiesiny, ciecz spełniająca rolę smaru między cząstkami zawiesiny zostaje wyparta i opory ścinania rosną.
Ciecze o własnościach reologicznych zmieniających się w czasie
Ciecz tiksotropowa - pod wpływem ścinania następuje rozpad struktury wewnętrznej. Im dłuższy czas działa naprężenie ścinające, tym większe następuje zniszczenie struktury. Pozostawienie cieczy tiksotropowej w spokoju powoduje odbudowę struktury wewnętrznej. Typowym przykładem cieczy tiksotropowej są smary plastyczne, których lepkość pozorna zmniejsza się, gdy poddamy je oddziaływaniom mechanicznym. Ciecz tiksotropowa można uważać za taką ciecz pseudoplastyczna, której uporządkowanie cząsteczek podczas przepływu zachodzi w czasie.
Ciecze reopeksyjne - pod wpływem ścinania następuje tworzenie struktury wewnętrznej. Z cieczami takimi spotykamy się w praktyce bardzo rzadko.
Ciecze lepkosprężyste. Do tej grupy cieczy należą ciecze o bardzo dużej lepkości, a równocześnie wykazujące pewne własności sprężyste. Przykładem takiego rodzaju cieczy mogą być różnego rodzaju żywice, smoły, asfalty, niektóre polimery itp. Ciecz lepkosprężysta jako bardzo lepka ciecz zachowuje się zgodnie z prawem Newtona, a ze względu na własności sprężyste - również z prawem Hooke'a.
6.2.2. Jednostki lepkości
Opierając się na wzorze Newtona można lepkość określić następującym wzorem
Jednostką lepkości dynamicznej, określoną na podstawie powyższego wzoru za pomocą jednostek układu CGS, jest l puaz (l P). Ciecz ma lepkość jednego puaza wówczas, gdy dwie warstewki cieczy o powierzchni l cm², oddalone od siebie o l cm, pod działaniem siły l dyny poruszają się z prędkością l cm/s.
W układzie CGS jednostkę lepkości dynamicznej określa się więc z zależności
|
[ |
|
] |
| |
1 P = |
[ |
dyna • s cm² |
] |
= |
= |
[ |
g cm • s |
]
| (6.8)
|
W układzie SI jednostką lepkości dynamicznej jest paskalosekunda
|
1 Pa • s = |
[ |
N • s m² |
] |
= |
[ |
kg m •s |
]
| (6.9)
|
Ponieważ paskalosekunda Pa • s jest jednostką dużą, dlatego też w praktyce używa się jednostki 1000 razy mniejszej zwanej milipaskalosekundą mPa- s
1 mPa • s = 1 cP
Odwrotność lepkości dynamicznej h nazywa się płynnością F
|
F = |
1 h |
[ |
cm • s g |
] |
= |
[ |
10 m • s kg |
]
| (6.10)
|
W obliczeniach hydrodynamicznych posługujemy się najczęściej lepkością kinematyczną
gdzie q - gęstość cieczy.
Jednostką lepkości kinematycznej w układzie CGS jest l stokes (St).
Ciecz ma lepkość l St, jeżeli jej gęstość jest równa l g/cm³ i do wzajemnego przesunięcia z prędkością l cm/s dwóch jej warstw o powierzchni l cm² odległych od siebie o l cm trzeba użyć siły l dyny
|
1 St = |
[ |
g cm³
|
] |
= |
[ |
cm² s |
] |
= |
[ |
10-4 m² s |
]
| (6.12)
|
Częściej używane są jednostki mniejsze, centistokesy (cSt) i milistokesy (mSt).
W układzie SI wymiarem lepkości kinematycznej jest: m²/s = 104 • St = 106 cSt (l cSt = 1 mm ²/s). Lepkość wyrażona w jednostkach układu CGS lub SI nazywa się lepkością bezwzględną.
Dla celów praktycznych, gdy chodzi tylko o porównanie cieczy posługujemy się pojęciem lepkości względnej lub lepkości umownej.
Lepkość względna może być liczbą bezwymiarową, gdy np.: porównuje się lepkość dynamiczną danej cieczy z lepkością dynamiczną cieczy wzorcowej, np. wody:
gdzie: hc - lepkość dynamiczna cieczy w temperaturze tc w Pa • s, hw - lepkość dynamiczna cieczy wzorcowej (wody) w temperaturze tw w Pa • s.
Jeżeli lepkość względna jest wyrażona jako stosunek lepkości dynamicznej cieczy do lepkości dynamicznej wody w temperaturze 20,2°C, to wtedy liczbowo równa się lepkości dynamicznej danej cieczy wyrażonej w mPa • s, gdyż w temperaturze 20,2°C lepkość dynamiczna wody jest równa l mPa • s.
Najczęściej jednak lepkość wyraża się w jednostkach umownych, które stanowią zwykle stosunek czasu wypływu badanej cieczy do czasu wypływu cieczy wzorcowej w ściśle znormalizowanych warunkach pomiaru lub po prostu określają czas wypływu badanej cieczy ze znormalizowanego aparatu w znormalizowanych warunkach.
W Polsce i w większości krajów europejskich, lepkość względną określa się za pomocą stopni Englera (°E). Lepkość w stopniach °E jest to stosunek czasu wypływu 200 cm³ badanej cieczy w danej temperaturze do czasu wypływu tej samej ilości wody destylowanej w temperaturze 20°C przez znormalizowaną kapilarę aparatu Englera.
W Wielkiej Brytanii i USA określa się lepkość względną za pomocą sekund Redwooda. Jest to czas wypływu 50 cm³ badanej cieczy w sekundach. Ponieważ istnieją dwa rodzaje lepkościomierzy Redwooda, rozróżnia się dwa rodzaje sekund Redwooda (sekundy Redwooda handlowe i sekundy Redwooda Admirality). We Francji stosowane są stopnie Barbe (°B), które określają ile cm³ cieczy wypłynie w ciągu godziny z lepkościomierza Barbego.
W USA powszechnie stosowane jest wyrażenie lepkości za pomocą sekund Saybolta określających czas wypływu 60 cm³ badanej cieczy z lepkościomierza Saybolta.
Ponieważ lepkościomierz ma 2 wymienne kapilary, z których jedną stosuje się dla cieczy o małej lepkości, a drugą dla cieczy o dużej lepkości, rozróżnia
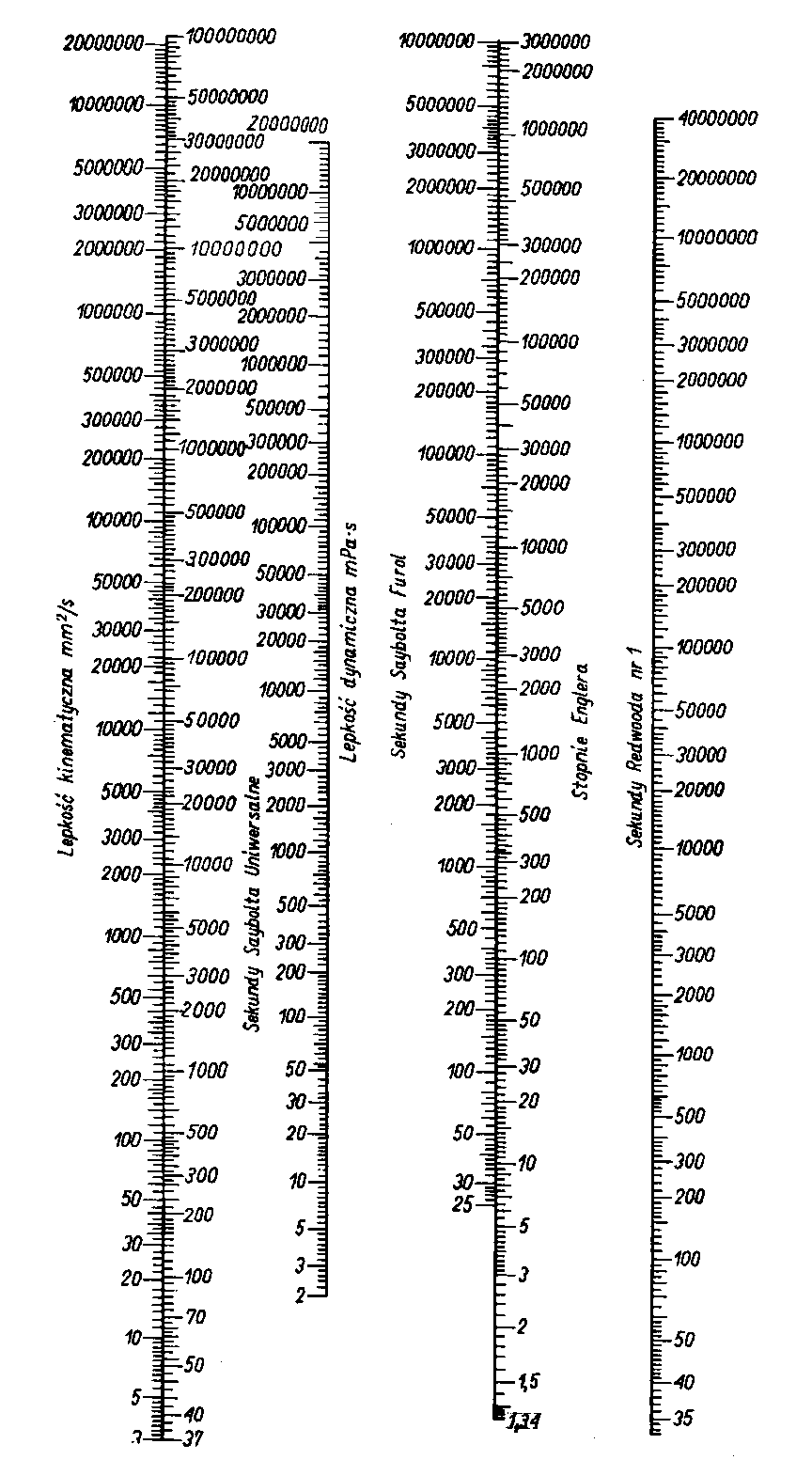 |
Rys. 6.9. Nomogram do przeliczania jednostek lepkości
|
Tablica 6.2. Przeliczanie jednostek lepkości
Lepkość ki- nematyczna mm²/s | Lepkość względna | w stopniach Englera (°E) |
w sekundach Saybolta Uniwersalnych (S.U.S) w temperaturze | w sekundach Redwooda (handlowe) w temperaturze |
37,8° (100°F) | 54,4°C (130°F) | 98,9°C (210°F) | 21,1°C (70°F) | 60°C (140°F) | 93,3°C (200°F) |
2 | 32,0 | 32,7 | 32,8 | 30,2 | 31,0 | 31,2 | 1,140 |
3 | 36,0 | 36,1 | 36,3 | 32,7 | 33,4 | 33,7 | 1,224 |
4 | 39,1 | 39,2 | 39,4 | 35,3 | 35,9 | 36,3 | 1,308 |
5 | 42,3 | 42,4 | 42,6 | 37,9 | 38,5 | 38,9 | 1,400 |
6 | 45,5 | 45,6 | 45,8 | 40,5 | 41,1 | 41,5 | 1,481 |
7 | 48,7 | 48,8 | 49,0 | 43,2 | 43,7 | 44,1 | 1,563 |
8 | 52,0 | 52,1 | 52,4 | 46,0 | 46,3 | 46,9 | 1,653 |
9 | 55,4 | 55,5 | 55,8 | 48,9 | 49,1 | 49,7 | 1,746 |
10 | 58,8 | 58,9 | 59,2 | 51,7 | 52,0 | 52,6 | 1,837 |
11 | 62,3 | 62,4 | 62,7 | 54,8 | 55,0 | 55,6 | 1,928 |
12 | 65,9 | 66,0 | 66,4 | 57,9 | 58,1 | 58,7 | 2,020 |
13 | 69,6 | 69,7 | 70,1 | 61,0 | 61,3 | 61,9 | 2,120 |
14 | 73,4 | 73,5 | 73,9 | 64,4 | 64,6 | 65,2 | 2,219 |
15 | 77,2 | 77,3 | 77,7 | 67,7 | 67,9 | 68,7 | 2,323 |
16 | 81,1 | 81,3 | 81,7 | 71,0 | 71,4 | 72,2 | 2,434 |
17 | 85,1 | 85,3 | 85,7 | 74,7 | 74,9 | 75,8 | 2,540 |
18 | 89,2 | 89,4 | 89,8 | 78,1 | 78,5 | 79,4 | 2,644 |
19 | 93,3 | 93,5 | 94,0 | 81,7 | 82,1 | 83,1 | 2,755 |
20 | 97,5 | 97,7 | 98,2 | 85,4 | 85,8 | 86,9 | 2,870 |
21 | 101,7 | 101,9 | 102,4 | 89,2 | 89,5 | 90,7 | 2,984 |
22 | 106,0 | 106,2 | 106,7 | 92,9 | 93,3 | 94,5 | 3,10 |
23 | 110,3 | 110,5 | 111,1 | 96,7 | 97,1 | 98,3 | 3,22 |
24 | 114,6 | 114,8 | 115,4 | 100,4 | 100,9 | 102,2 | 3,34 |
25 | 118,9 | 119,1 | 119,7 | 104,2 | 104,7 | 106,1 | 3,46 |
26 | 123,3 | 123,5 | 124,2 | 108,1 | 108,6 | 110,0 | 3,58 |
27 | 127,7 | 127,9 | 128,6 | 111,9 | 112,5 | 114,0 | 3,70 |
28 | 132,1 | 132,4 | 133,0 | 115,8 | 116,5 | 118,0 | 3,82 |
29 | 136,5 | 136,8 | 137,5 | 119,7 | 120,4 | 122,0 | 3,95 |
30 | 140,9 | 141,2 | 141,9 | 123,7 | 124,4 | 126,0 | 4,07 |
31 | 145,3 | 145,6 | 146,3 | 127,5 | 128,3 | 130,1 | 4,20 |
32 | 149,7 | 150,0 | 150,8 | 131,5 | 132,3 | 134,1 | 4,32 |
33 | 154,2 | 154,5 | 155,3 | 135,4 | 136,3 | 138,1 | 4,45 |
34 | 158,7 | 159,0 | 159,8 | 139,3 | 140,2 | 142,2 | 4,57 |
35 | 163,2 | 163,5 | 164,3 | 143,3 | 144,2 | 146,2 | 4,70 |
36 | 167,7 | 168,0 | 168,9 | 147,2 | 148,2 | 150,3 | 4,83 |
37 | 172,2 | 172,5 | 173,4 | 151,2 | 152,2 | 154,2 | 4,96 |
38 | 176,7 | 177,0 | 177,9 | 155,2 | 156,2 | 158,3 | 5,08 |
39 | 181,2 | 181,5 | 182,5 | 159,2 | 160,3 | 162,5 | 5,21 |
40 | 185,7 | 186,0 | 187,0 | 163,2 | 164,3 | 166,7 | 5,34 |
- Uwaga:
- Wartość lepkości kinematycznej nie zależy od temperatury w jakiej została wyznaczona (tak np. 10 mm²/s jest zawsze 10 mm²/s), lepkość względna natomiast zwłaszcza ta, która jest równa czasowi wypływu cieczy z aparatu, zależy nieznacznie od temperatury pomiaru (rozszerzalność cieplna aparatu, dyszy wypływowej itp.). Dla lepkości względnej w °E błędy wynikające z różnic temperatury są zmniejszone w znacznym stopniu przez odnoszenie czasu wypływu oleju do czasu wypływu wody.
| |
się dwa rodzaje sekund Saybolta. Saybolt Uniwersal Seconds i Saybolt Furol Seconds (SUS i SFS). W celu przeliczenia jednostek umownych na jednostki bezwzględne stosowane są różnego rodzaju zależności przedstawione za pomocą empirycznych wzorów lub nomogramów.
Wykres na rys. 6.9 jest stosowany do przeliczania poszczególnych rodzajów jednostek umownych na jednostki bezwzględne.
Nomogramy i podane wzory przeliczeniowe mają jedynie charakter mniej lub więcej przybliżony i gdy chodzi o dużą dokładność w określeniu lepkości, należy ją określać bezpośrednio w jednostkach bezwzględnych (tabl. 4.2).
6.2.3. Pomiary lepkości
Ciecz przeciwstawia się przesuwaniu jej warstewek względem siebie zarówno przy ruchu cieczy względem dowolnego ciała znajdującego się w tej cieczy, jak i ruchu tego ciała względem cieczy. Obydwa przypadki wykorzystane są do mierzenia lepkości. W celu dokładnego wyznaczenia lepkości cieczy przy jej ruchu, ruch ten powinien być ruchem warstwowym, a przynajmniej jak najbardziej zbliżonym do tego rodzaju ruchu. Ruch taki odbywa się jedynie przy małych prędkościach w przewodach o bardzo małej średnicy (zwanych kapilarami).
Pomiar lepkości, wykorzystujący przepływ cieczy przez kapilary, opiera się na prawie Hagena-Poiseuille'a
gdzie: r - promień kapilary w cm, l - długość kapilary w cm, t - czas płynięcia w s, Dp - różnica ciśnień powodująca przepływ cieczy w Pa, V - objętość cieczy przepływającej w czasie t w cm³.
Jeżeli ciecz przepływa przez kapilarę tylko pod działaniem własnego ciężaru, wówczas różnicę ciśnienia Dp wyraża się wzorem
gdzie: h1 - h2 - różnica poziomów cieczy w cm, r -gęstość cieczy w g/cm³, g - przyspieszenie grawitacyjne w cm/s².
Zatem wzór (6.14) przybierze postać
|
h = |
pr4 ( h1 - h2 ) g 16 l V |
r t
| (6.16)
|
Jeżeli przyjmie się
|
pr4 ( h1 - h2 ) g 16 l V |
= K
| (6.17)
|
to w rezultacie otrzyma się wzór o prostszej postaci
gdzie K - stała kapilary niezależna od temperatury.
Dzieląc obie strony równania przez r otrzymuje się wzór na lepkość kinematyczną
Tak więc w metodach opartych na przepływie cieczy przez kapilary, wystarcza przy pomiarze lepkości kinematycznej wyznaczyć jedynie czas przepływu cieczy przez kapilarę.
Spośród najbardziej rozpowszechnionych lepkościomierzy (wiskozymetrów) przepływowych należy wymienić lepkościomierze: Ostwalda, Ostwalda-Pinkiewicza, Vogel-0ssaga i Ubbelohde'a (rys. 6.10). Służą one do oznaczania lepkości kinematycznej dla celów eksploatacyjnych oraz naukowo-badawczych.
 |
Rys. 6.10. Lepkościomierze kapilarne:
- lepkościomierz Ostwalda-Pinkiewicza;
|
- lepkościomierz Vogel-0ssaga;
- - statyw,
- - łaźnia,
- - termometr,
- - lepkościomierz;
|
- - termostat,
- - zbiorniczek oleju,
- - kreski na kapilarze,
- - kreski na kapilarze,
- - oprawka z gwintem,
- - pokrywka,
- - wzierniki,
|
- - termometr oleju,
- - termometr termostatu,
- - pompka olejowa,
- - mieszadło powietrza,
- - palnik gazowy,
- - klucz do przykręcania kapilary
| | |
W przypadku ruchu ciał stałych w ośrodkach ciekłych w grę wchodzi jedynie tarcie wewnętrzne między warstewkami cieczy, ponieważ na powierzchni ciała stałego jest zaadsorbowana warstewka cieczy.
Do obliczania lepkości stosuje się wiele wzorów uwzględniających zarówno charakter ruchu i kształt poruszającego się ciała.
Przy opadaniu ciał kulistych stosuje się prawo Stokesa. Pomiar lepkości opartej na tej metodzie polega na zmierzeniu czasu opadania kulki o znanych wymiarach i gęstości, w badanym ośrodku ciekłym. Jeżeli kulka porusza się ze stałą prędkością w ośrodku ciekłym, to opór na skutek wewnętrznego tarcia cieczy można wg Stokesa wyrazić równaniem
gdzie: r - promień kuli w m, h - lepkość dynamiczna w Pa•s, v - prędkość opadania kulki w m/s.
Na kulkę opadającą w cieczy wypełniającej naczynie działają trzy siły: ciężar kulki Pk, wypór cieczy równy ciężarowi wypartej przez kulkę cieczy Pc i siła tarcia wewnętrznego cieczy P. Ciężar kulki Pk i wypór cieczy Pk wyraża się analogicznymi wzorami
|
Pk = |
4 3 |
p r ³ r k g
| (6.21)
| |
Pc = |
4 3 |
p r ³ r c g
| (6.22)
|
gdzie: g - przyspieszenie grawitacyjne w m/s², rc, rk -gęstość cieczy i gęstość materiału kulki w kg/m³.
Ze wzoru Stokesa wynika, że opór cieczy przeciwdziałający ruchowi kulki jest proporcjonalny do prędkości kulki. Po osiągnięciu przez kulkę odpowiedniej prędkości opór ten zrównoważy pozorny ciężar kulki. Od tej chwili ruch kulki będzie jednostajny
Po podstawieniu ze wzorów (6.20) do (6.22) odpowiednich wartości na P, Pk i Pc otrzymuje się
|
6 p r h v = |
4 3 |
p r ³ ( r k - r c ) g
| (6.24)
|
a stąd
|
h = |
2 r ² ( r k - r c ) g 9 v
| (6.25)
|
gdzie v - prędkość opadania kulki.
Podstawiając z kolei
|
v = |
l t |
i |
2 r ² g 9 l |
= K
| (6.26)
|
otrzymamy
|
h = |
2 r ² ( r k - r c ) g t 9 l
| (6.27)
|
lub
|
h = |
K ( r k - r c ) t
| (6.28)
|
gdzie: l - droga przebyta przez kulkę w m, t - czas opadania kulki w s, K - wielkość stała dla danego przyrządu.
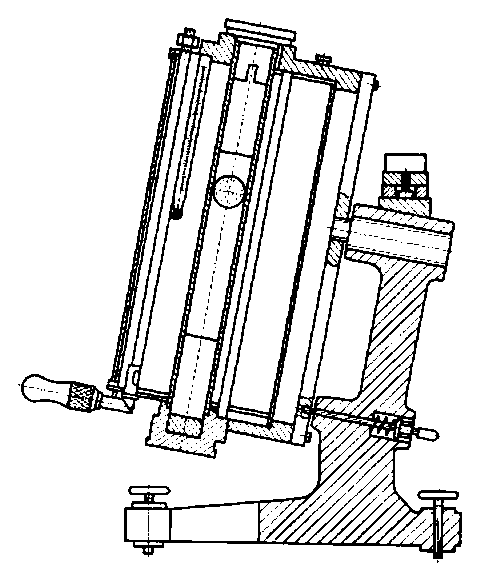 |
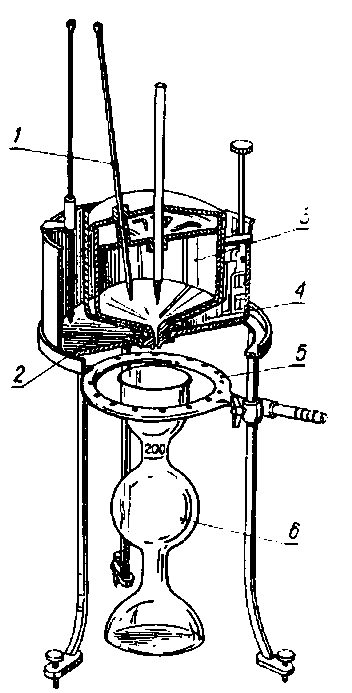 |
Rys. 6.11. Lepkościomierz Höplera |
Rys. 6.12. Lepkościomierz Englera:
- - termometr,
- - łaźnia wodna,
- - naczynie pomiarowe,
- - mieszadło,
- - palnik gazowy,
- - kolba
|
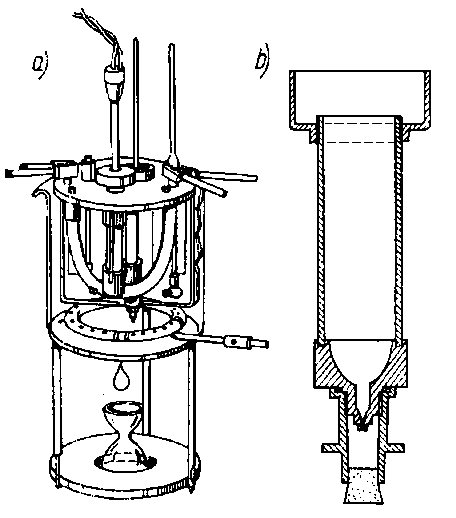 |
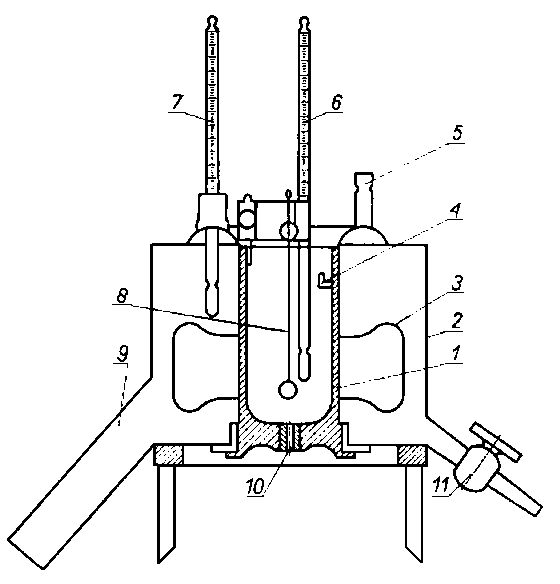 |
Rys. 6.13. Lepkościomierz Saybolta:
- widok ogólny,
- naczynie pomiarowe
|
Rys. 6.14. Lepkościomierz Redwooda;
- - naczynie na olej,
- - łaźnia grzejna,
- - mieszadło,
- - wskaźnik poziomu,
- - wlew,
- - termometr oleju,
- - termometr do łaźni,
- - zatyczka,
- - rękaw grzejny,
- - otwór wypływowy,
- - kurek spustowy
|
Praktycznie więc pomiar sprowadza się do zmierzenia czasu opadania odpowiednio dobranej kulki oraz na wyznaczeniu gęstości badanej cieczy.
Najbardziej rozpowszechnionym typem lepkościomierzy opartym na tej metodzie jest lepkościomierz Höplera (rys. 6.11).
Dla celów technicznych, zwłaszcza w przemyśle naftowym, opracowano wiele lepkościomierzy do szybkich i łatwych pomiarów lepkości względnej.
Lepkościomierze tego typu odznaczają się dużą trwałością i prostą obsługą. Pomiar lepkości jest oparty na wyznaczeniu czasu wypływu badanej cieczy przez kalibrowany otwór z naczynia o określonej pojemności (rys. 6.12, 6.13 i 6.14).
Wszystkie typy lepkościomierzy mają łaźnie pozwalające utrzymywać stałą temperaturę podczas pomiaru. Istnieją jeszcze inne sposoby pomiarów lepkości olejów rzadziej stosowane, oparte na zanikaniu wahań ciała stałego w badanej cieczy, na tłumieniu drgań skrętnych tarczy zanurzonej w badanej cieczy, na zasadzie pomiaru oporu stawianego cieczy obracającemu się w niej walcowi itp. Do pomiarów cieczy o konsystencji półstałej (lepkość 105 - 1014 mPa) służą konsystometry (najczęściej Höplera rys. 6.15). Pomiar polega na oznaczeniu czasu i drogi, którą przebędzie kulka odpowiednio obciążona i zanurzona w badanej substancji o określonej temperaturze.
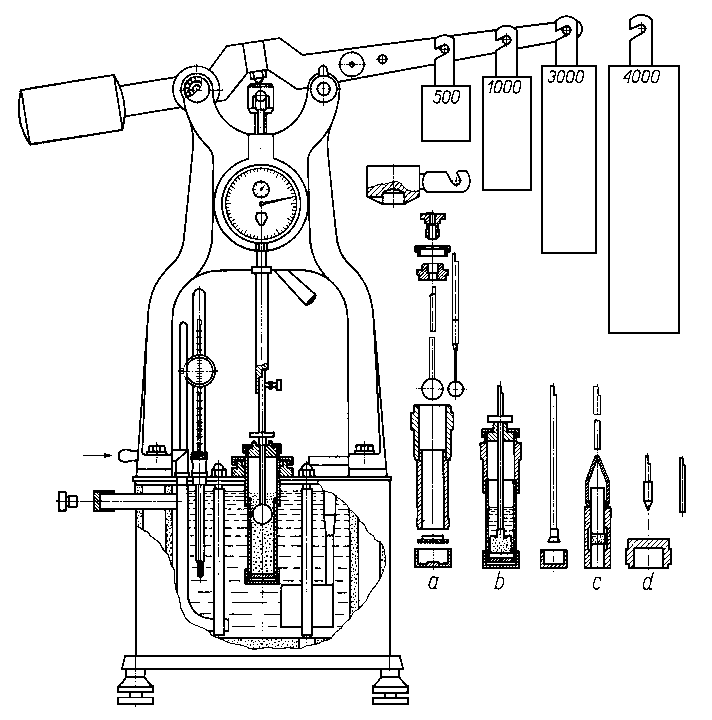 |
Rys. 6.15. Konsystometr Höplera:
- urządzenie do wyznaczania lepkości normalnej,
- urządzenie do wyznaczania lepkości strukturalnej,
- urządzenie do wyznaczania modułu elastyczności,
- urządzenie do wyznaczania twardości
|
Przyrządy te umożliwiają również wyznaczanie granicznych naprężeń ścinających w przypadku układów koloidalnych.
6.2.4. Zależność lepkości od ciśnienia
Wywarcie na ciecz ciśnienia powoduje zbliżenie jej cząsteczek do siebie i zwiększenie oddziaływań międzycząsteczkowych powodujące zwiększenie lepkości. Wpływ ciśnienia na lepkość przedstawiono schematycznie na rys. 6.16. Małe ciśnienie powoduje nieznaczny wzrost lepkości, przy większym ciśnieniu przyrost ten jest znaczny.
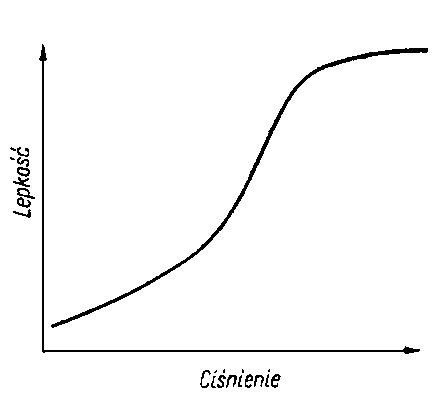 |
Rys. 6.16. Zależność lepkości od ciśnienia
|
Przy ciśnieniach rzędu kilku tysięcy MPa zaznacza się już wpływ odpychania międzycząsteczkowego i krzywa przyrostu lepkości ze wzrostem ciśnienia staje się bardziej płaska, zbliżając się asymptotycznie do pewnej stałej wartości.
Rozpatrywanie zależności lepkości od ciśnienia nie jest zagadnieniem wyłącznie teoretycznym, lecz ma duże znaczenie praktyczne. W skojarzeniach trących maszyn bardzo często występują ciśnienia rzędu kilku tysięcy MPa. W przekładniach zębatych naciski w obszarach zazębienia osiągają wartość kilkuset, a nawet kilku tysięcy MPa. Najczęściej przyjmuje się, że do około 25 MPa zależność ta ma charakter liniowy i do obliczenia zmian lepkości w tych zakresach można się posłużyć wzorem
|
hp = ho ( 1 + a p )
| (6.29)
|
gdzie: hp - lepkość dynamiczna przy ciśnieniu p w Pa • s, ho - lepkość dynamiczna przy ciśnieniu atmosferycznym w Pa • s, a - stała dla danego oleju.
Dla ciśnień powyżej 25 MPa zaznacza się bardzo znaczny przyrost lepkości i stosuje się wzory uwzględniające wykładniczą zależność lepkości od ciśnienia
lub wzór Barusa
gdzie: a - stała (dla olejów mineralnych rzędu 1,002-1,004, dla olejów roślinnych i zwierzęcych rzędu 1,001-1,0015, gdy p jest w kG/cm² ), a - ciśnieniowy współczynnik lepkości w 1/Pa.
Ostatni wzór jest najczęściej stosowany w rozważaniach teoretycznych. Ze względu na duże znaczenie praktyczne zależności lepkości od ciśnienia, przeprowadzono w różnych ośrodkach szczegółowe badania dla olejów z ropy naftowej i różnych cieczy stosowanych do smarowania maszyn. W roku 1953 ukazało się na ten temat obszerne sprawozdanie Amerykańskiego Stowarzyszenia Inżynierów Mechaników - ASME (13). Badania prowadzono aż do zakresu ciśnień 980,665 • 106 Pa w temperaturze 0°C. 25°C, 37,7°C, 99°C, 218°C. Okazało się, że wzór wykładniczy daje dobre rezultaty tylko w zakresie umiarkowanych ciśnień, natomiast przy wysokich ciśnieniach wartości lepkości olejów obliczone z wzoru wykładniczego i zmierzone, różnią się 500 razy. Znaczne różnice występują również w różnych zakresach
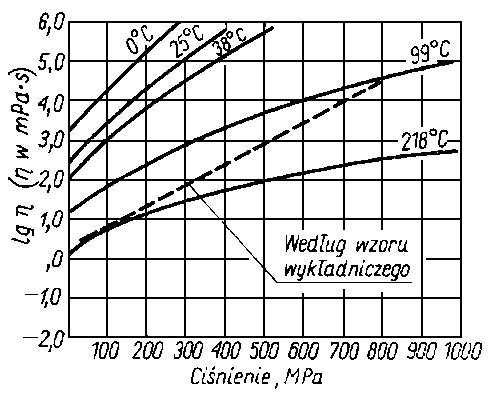 |
Rys. 6.17. Zależność lepkości od ciśnienia dla oleju 32G (krzywe wyznaczone eksperymentalnie i krzywa obliczona)
|
temperatury, czego wzór wykładniczy nie uwzględnia (rys. 6.17). Różnice te uwydatniają się zwłaszcza w przypadku olejów o charakterze parafinowym.
Hersey i Hopkins (24) wykonali dla ASME studium problemu zależności lepkości od ciśnienia ze sprawozdaniem z wyników badań oraz pełnym bardzo szczegółowym opracowaniem literatury. Obszerne badania nad zależnością lepkości od ciśnienia przeprowadzono w Laboratorium Ciśnieniowym Instytutu Naftowego w Hanowerze (Institut für Erdolforschung) przez Kussa (27). Kuss zmodyfikował równanie wykładnicze wprowadzając wzór
|
hp = ho e( a p + b p² )
| (6.32)
|
gdzie: hp, ho - jak we wzorze (6.29), a, b współczynniki mające różne wartości dla różnych olejów (a w 1/Pa, b w 1/Pa²).
F. Hotte (17) sprawdził przydatności istniejących wzorów i rozrzut błędów, jakie powstają przy obliczeniach w stosunku do pomiarów dla 413 substancji (147 czystych substancji, 68 olejów syntetycznych i 198 olejów z ropy naftowej).
Wzór na zależność lepkości od ciśnienia opracował również Blok
|
lg |
hp ho |
= B lg ( 1 + |
p b |
)
| (6.33)
|
gdzie: b, B stale dla danego oleju przy określonej temperaturze.
Roelands podał trzy wzory na zależność lepkości od ciśnienia
|
lg |
hp ho |
= |
K1p 1 + c1p
| (6.34)
|
|
lg hp = ( lg ho +1,2) • (1 + |
p 2000 |
) | z
| (6.36)
|
gdzie: K1, c1, K2, c2, z - stałe dla danego oleju przy określonej temperaturze.
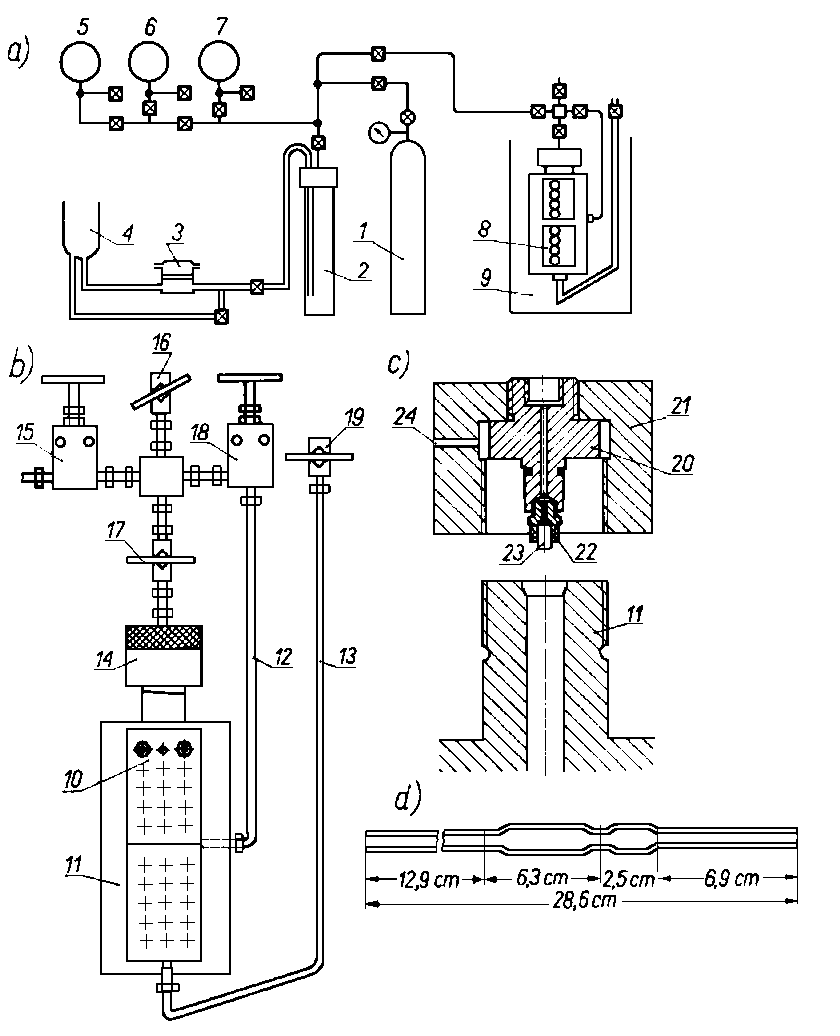 |
Rys. 6.18. Urządzenie do pomiaru lepkości przy wysokim ciśnieniu: |
a) schemat urządzenia pomiarowego;
1 - zasilająca butla gazowa,
2 - pojemnik manipulacyjny,
3 - pompa oleju,
4- zbiornik oleju,
5 do 7 - zawory wysokociśnieniowe,
8 - lepkościomierz ciśnieniowy,
9 - łaźnia do utrzymania stałej temperatury; |
b) lepkościomierz ciśnieniowy;
10-okienka wziernikowe,
11 - pojemnik ciśnieniowy,
12 - przewód wyrównawczy,
13 - przewód napełniania,
14 - głowica zamykająca,
15 do 19 - zawory ciśnieniowe; |
c) głowica zamykająca (14);
20 - wewnętrzna głowiczka ciśnieniowa,
21 - zdejmowana przykrywka,
22 - uchwyt kapilarny,
23 - kapilara,
24-zawór bezpieczeństwa;
d) kapilara (23)
|
Wielu autorów, jak Witt (16), Roelands, Noack (25) opracowało wzory uwzględniające równocześnie zależność lepkości od ciśnienia i temperatury. Ma to szczególnie duże znaczenie przy określeniu zachowania się oleju w węzłach tarcia. Bardzo wnikliwe badania nad zależnością lepkości od ciśnienia przeprowadził Cameron (7). Stwierdził on, że wzór wykładniczy Barusa (6.31) może scharakteryzować zależność od ciśnienia tylko dla olejów o charakterze naftenowym (punkt anilinowy poniżej 90°C). Współczynnik ciśnieniowy lepkości a można obliczyć z zależności
|
a = ( 0,6 + 0,9565 lg ho ) • 10-8 1/Pa
| (6.37)
|
gdzie ho - lepkość dynamiczna przy ciśnieniu atmosferycznym w mPa • s.
Dla olejów o charakterze parafinowym (punkt anilinowy powyżej 90°C) Cameron ustalił następującą zależność
|
(lg hp )3/2 = m ( p + b )
| (6.38)
|
przy czym stałą m można obliczyć ze wzoru
|
m = (1,3 +7,1 lg ho ) • 10-2
| (6.39)
|
a stałą b z zależności (lg ho)3/ = m b, a dla lepkości ho powyżej 6 mPa • s wystarczająco dokładna jest zależność:
gdzie: ho - w mPa • s, p - w tysiącach funtów/cal² (funt/cal² = 6,896 • 10³ Pa), b - w cal²/1000 funtów.
Lepkość przy wysokich ciśnieniach wyznacza się w ciśnieniowych kapilarnych lepkościomierzach (rys. 6.18). Przy pomiarach lepkości pod ciśnieniem rzędu kilku tysięcy MPa Cameron stosował metodę optyczną (prążki interferencyjne).
6.2.5. Zależność lepkości od temperatury
6.2.5. l. Zmienność lepkości cieczy wraz ze zmianami temperatury
Lepkość cieczy wraz ze wzrostem temperatury maleje, natomiast lepkość gazów rośnie. Obniżenie temperatury powoduje odwrotny skutek. Wyjaśnienia tego zjawiska należy szukać w charakterze ruchu poszczególnych cząsteczek oraz działających na nie sił. Im wyższa jest temperatura, tym większa jest energia kinetyczna cząsteczek i tym większe prawdopodobieństwo wystąpienia bezładnych zderzeń cząsteczek, co powoduje zwiększenie lepkości, czyli oporów tarcia wewnętrznego.
Przy podwyższaniu temperatury wzrasta jednocześnie odległość między poszczególnymi cząsteczkami. Jest to równoznaczne ze zmniejszeniem wzajemnego oddziaływania, a więc zmniejszeniem lepkości. Jeżeli cząsteczki występują w ośrodku blisko siebie, jak w cieczach, zasadniczą rolę w zmianach lepkości spełnia oddalenie cząsteczek od siebie. W miarę większego oddalania cząsteczek, oddziaływanie między nimi maleje szybko do zera i wtedy dominujący wpływ na lepkość ma ruch cieplny. Obserwuje się to w gazach, których lepkość wzrasta z podwyższeniem temperatury.
Jak widać z powyższego rozważania, na zmianę lepkości cieczy wraz ze zmianami temperatury ma wpływ przede wszystkim wzajemne oddziaływanie cząsteczek. Ogólnie rzecz biorąc im cząsteczki cieczy są większe i im bliżej siebie, tym ciecz ma większą lepkość. Tym też tłumaczy się wpływ ciśnienia na lepkość (zmniejszenie odległości cząsteczek) oraz wpływ ilości i wielkości cząsteczek, a więc wpływ asocjacji na lepkość.
Dotychczas nie udało się ustalić ogólnej zależności między lepkością a masą cząsteczkową cieczy oraz zmienności lepkości wraz ze zmianami temperatury.
6.2.5.2. Zmienności lepkości olejów wraz ze zmianami temperatury
Oleje smarne podobnie jak inne ciecze zmieniają swoją lepkość wraz ze zmianą temperatury. Zjawisko to może powodować groźne w skutkach konsekwencje podczas eksploatacji urządzeń ze względu na zaburzenia w procesie smarowania. Zmniejszenie lepkości oleju, a więc zmniejszenie oporów tarcia wewnętrznego, ułatwia wyciskanie oleju spomiędzy trących elementów maszyn. Może to doprowadzić do zatarcia, a więc zniszczenia urządzenia. Wzrost lepkości przy obniżaniu temperatury eksploatacji powoduje wzrost strat na pokonywanie tarcia wewnętrznego cieczy. Może to doprowadzić również do trudności w uruchamianiu maszyny lub też to uruchomienie uniemożliwić.
Jeżeli olej oprócz funkcji cieczy smarującej spełnia również funkcje cieczy roboczej w różnego rodzaju serwomechanizmach, układach automatycznych sterowania lub układach hydraulicznych, wówczas zmiana jego lepkości może spowodować poważne zaburzenia w pracy tych urządzeń. Z tego względu ciecz smarująca powinna, charakteryzować się możliwie najmniejszą zmiennością lepkości w zakresie temperatury występującej w czasie eksploatacji danego urządzenia. Tak więc dla eksploatującego ważna jest nie tylko odpowiednio dobrana lepkość oleju, ale również jej zmiany wraz ze zmianami temperatury. Im mniejsze zmiany lepkości wykazuje dany olej, tym wyższa jest jego wartość użytkowa.
Zakwalifikowanie oleju jako cieczy smarującej z określonym przeznaczeniem eksploatacyjnym wymaga zorientowania odbiorcy nie tylko w lepkości oleju, ale również w jej zmianach wraz ze zmianami temperatury.
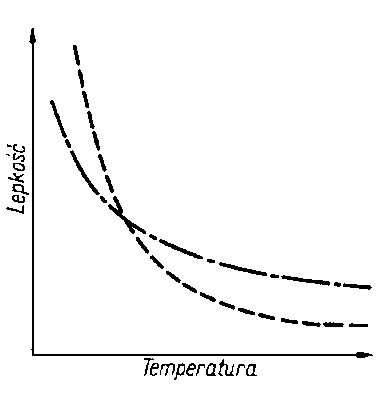 |
Rys. 6.19. Dwie przykładowe krzywe zależności lepkości od temperatury
|
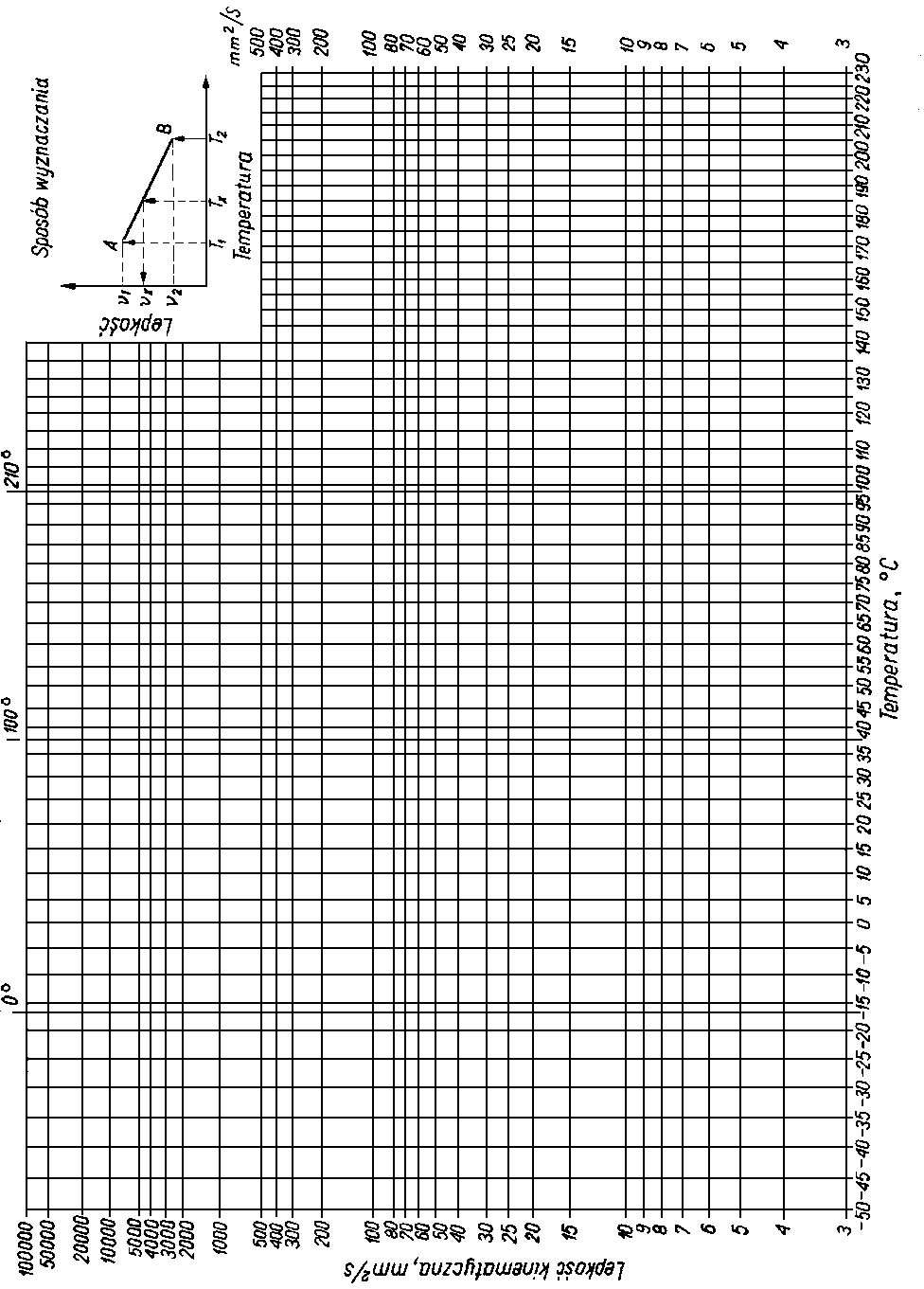 |
Rys. 6.20. Nomogram do wyznaczania lepkości oleju w zależności od temperatury
|
Zależność lepkości oleju od temperatury można przedstawić w postaci wzoru lub wykresu. Obydwie formy są do codziennych celów praktycznych zbyt skomplikowane i wymagają pewnego przygotowania teoretycznego. Zarówno w czasie produkcji, jak i do celów eksploatacyjnych, konieczne jest przedstawienie tej zależności w postaci możliwie najprostszej, zrozumiałej nawet dla niewykwalifikowanego personelu, a równocześnie jednoznacznej. Najlepszym sposobem byłoby przedstawienie tej zależności za pomocą jakiejś jednej liczby charakterystycznej.
Przy graficznym przedstawieniu wyników oznaczeń lepkości oleju w różnych temperaturach otrzymuje się krzywą wykładniczą (rys. 6.19).
Matematycznie zależność lepkości od temperatury przedstawia wzór Walthera (38)
gdzie: nt - lepkość kinematyczna w mm²/s, T - temperatura w K, c, k, m - stałe.
Po zlogarytmowaniu otrzymuje się
|
m lg T + lg lg (nt + c) = lg lg k
| (6.42)
|
W literaturze i normach (DIN) przyjmuje się c = 0,8, w normach amerykańskich c -= 0,65 - 0,75. W zależności od charakteru chemicznego i masy cząsteczkowej oleju odpowiednio dobrane wartości c zapewniają uzyskanie wyników obliczeń zgodnych z wynikami pomiarów.
Jeżeli przyjmie się lg lg k = A i m = B, c = 0,8, to
|
lg lg (nt + 0,8) = A - B lg T
| (6.43)
|
Po graficznym przedstawieniu zależności lepkości od temperatury otrzymuje się w układzie logarytmicznym, linię prostą nachyloną do osi temperatury pod pewnym kątem. Im kąt ten jest mniejszy, tym olej ma lepkość wykazującą mniejsze zmiany przy zmianach temperatury, a więc jest lepszy. W Stanach Zjednoczonych A.P. wykres taki nazywa się wykresem lepkości ASTM, a kąt nachylenia - kątem nachylenia prostej ASTM (ASTM - Slope).
Wzór Walthera służy do wyznaczenia prostej lepkości w układzie logarytmicznym, gdy jest znana lepkość oleju w co najmniej dwóch temperaturach. Z wyznaczonej prostej można znaleźć wartości lepkości dla temperatury, w której nie była ona mierzona. Opierając się na wzorze Walthera skonstruowano wykres w układzie współrzędnych IgTi lglg(ł'+0,8) służący do wyznaczania lepkości oleju w różnych temperaturach (rys. 6.20).
Nachylenie prostej lepkości m można obliczyć z następującej zależności
|
m = tg a = |
lg lg (n1 + 0,8) - lg lg (n2 + 0,8) lg T1 - lg T2
| (6.44)
|
Oznaczając
|
w = lg lg (n + 0,8)
| (6.45)
|
otrzymamy
|
m = |
w1 - w2 lg T1 - lg T2
| (6.46)
|
Znając lepkość w dwóch temperaturach T1 i T2 można obliczyć lepkość w temperaturze T3 (K), wykorzystując zależność
|
w3 = m ( lg T1 - lg T3 ) + w1 = |
w1 - w2 lg T1 - lg T2 |
( lg T1 - lg T3 ) + w1
| (6.47)
|
W tabl. 6.3 przedstawiono dokładność wyników uzyskiwanych z obliczeń. W podwyższonych temperaturach dokładność jest zadowalająca, natomiast w niskich temperaturach odchylenia są znaczne.
Tablica 6.3. Różnice między wartościami lepkości dwóch olejów obliczonych z wzoru Walthera a zmierzonymi
Temperatura °C | Olej 1 | Olej 2 |
lepkość kinematyczna, mm²/s | lepkość kinematyczna, mm²/s |
zmierzona | obliczona | różnica | zmierzona | obliczona | różnica |
-17,7 | 2900 | 2300 | +600 | 3300 | 5300 | -2000 |
25 | 173,10 | 165,00 | +8,10 | 193,10 | 192,00 | +1,10 |
38 | 95,91 | - | - | 98,43 | - | - |
55 | 52,29 | 53,0 | -0,71 | 48,29 | 49,00 | -0,71 |
99 | 16,67 | - | - | 12,91 | - | - |
121 | 11,61 | 11,10 | +0,51 | 8,44 | 8,10 | +0,34 |
149 | 7,73 | 7,20 | +0,53 | 5,36 | 5,10 | +0,26 |
177 | 5,47 | 5,10 | +0,37 | 3,76 | 3,52 | +0,24 |
205 | 4,00 | 3,80 | +0,20 | - | - | -
| |
6.2.5.3. Wysokość biegunowa
Jeżeli wykreśli się w układzie logarytmicznym proste lepkości dla wielu olejów otrzymanych z tej samej ropy, to po odpowiednim przedłużeniu w zakres niskiej temperatury proste te przetną się w jednym punkcie. Punkt ten zwany jest biegunem lepkości, rzędna tego punktu nazywa się wysokością biegunową (rys. 6.21). Wysokość biegunowa jest to lepkość jaką mają oleje tego samego pochodzenia w biegunie lepkości. Jeżeli podobne wykresy sporządza się dla olejów otrzymanych z innej ropy, to otrzyma się nową wiązkę prostych mających również swój biegun. Różne serie olejów będą więc miały różne bieguny lepkości leżące w przybliżeniu na jednej prostej zwanej prostą biegunową. Im większa jest wartość wysokości biegunowej, tym większa zmienność lepkości wraz ze zmianami temperatury olejów należących do danej serii. Wysokość biegunowa określa więc pochodzenie oleju niezależnie od jego lepkości.
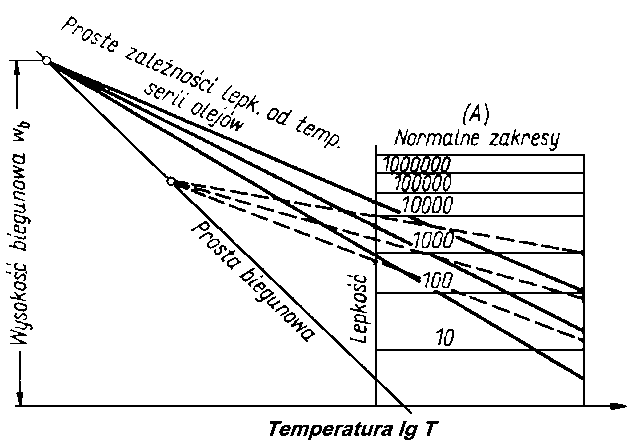 |
Rys. 6.21. Zależności lepkości od temperatury; wysokość biegunowa; A -obszar zależności lepkości od temperatury zwykle przedstawiany na wykresach
|
Wysokość biegunową Wb można wyznaczyć z wykresu lub też obliczyć ze wzoru znając lepkość w dwóch dowolnych temperaturach
|
Wb = |
m ( lg T1 - 2,410 )+ w1 1 - 0,194 m
| (6.48)
|
6.2.5.4. Wskaźnik lepkości (indeks wiskozowy)
Wskaźnik lepkości jest wielkością charakteryzującą zmiany lepkości wraz ze zmianami temperatury. Jest to wielkość bezwymiarowa, gdyż zmiany lepkości badanego oleju są odnoszone do zmian lepkości olejów wzorcowych. Wielkość tę wprowadzili Dean i Davis w roku 1929 (35). Stopniowo została ona znormalizowana przez Komitety Normalizacyjne większości państw. Dean i Davis otrzymali dwie serie olejów wzorcowych z dwóch rop różniących się między sobą w zasadniczy sposób składem chemicznym.
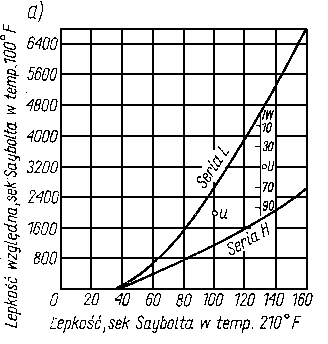
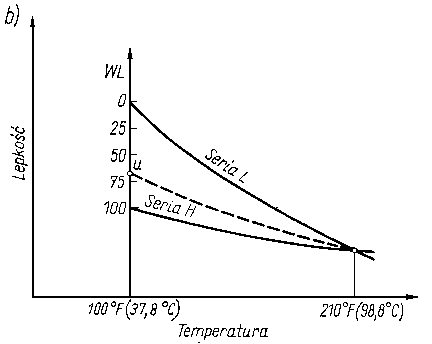 |
Rys. 6.22. Graficzne przedstawienie sposobu wyznaczania wskaźnika lepkości WL:
- a) w układzie lepkości w 100°F i 210°F,
- b) w układzie temperatura-lepkość
|
Serię olejów o małej lepkości, ale i o małych zmianach lepkości wraz ze zmianami temperatury otrzymano z ropy pensylwańskiej o charakterze parafinowym. Oleje te nazwano olejami serii H (H = high = wysoki), o wysokiej odporności na zmiany temperatury, i przyjęto dla nich umownie wartość wskaźnika lepkości równą 100 jednostek.
Drugą serię olejów o dużej lepkości, ale i o dużych zmianach lepkości otrzymano z ropy kalifornijskiej o charakterze naftenowo-aromatycznym. Oleje te nazwano olejami serii L (L = Iow = niski), o niskiej odporności na zmiany temperatury, i przyjęto dla nich umownie wartość wskaźnika lepkości równą zero.
Dla olejów obu serii oznaczono lepkość (w sekundach Saybolta) w temperaturze 100 i 210°F, a otrzymane wyniki naniesiono na wykres o współrzędnych lepkości w 210°F i lepkości w 100°F (rys. 6.22a).
Opierając się na współrzędnych punktów ustalono równania parabol dla obu serii olejów, umożliwiające obliczanie lepkości w temperaturze 100°F dla oleju o dowolnej lepkości, jeżeli jest znana jego lepkość w temperaturze 210°F.
Dla olejów serii H lepkość y w temperaturze 100°F
|
y = 0,0408 x ² + 12,568 x - 475,4
| (6.49)
|
a dla olejów serii L lepkość y w temperaturze 100°F
y = 0,02160 x² + 12,070 x - 721,2
gdzie: x - lepkość w temperaturze 210°F.
W ten sposób otrzymano krzywe dla wzorcowych serii olejów L i H. Umożliwia to porównywanie zmian lepkości badanego oleju U przy zmianach temperatury ze zmianami lepkości odpowiednich olejów serii wzorcowych.
Oznaczenie laboratoryjne lepkości badanego oleju U w temperaturze 100 i 210°F pozwala na znalezienie odpowiednich olejów wzorcowych. Odcinek rzędnej (rys. 6.22b) znajdujący się między dwoma krzywymi dzieli się na 100 części (dla oleju serii L wskaźnik lepkości WL = 0, a dla oleju serii H WL = 100).
Graficznie wskaźnik lepkości WL jest stosunkiem części rzędnej zawartej między krzywą L a punktem U, do części rzędnej zawartej między obu krzywymi L i H, czyli
|
WL = |
L - U L - H |
• 100
| (6.50)
|
Dean i Davis sporządzili tablicę określającą lepkości olejów wzorcowych od 40 do 160 sekund Saybolta w temperaturze 210°F.
W Polsce i wielu innych krajach wskaźnik lepkości wyznacza się opierając się na lepkości kinematycznej n50 i n100 wyrażonej w mm². Tablice dla olejów wzorcowych przeliczone zostały na odpowiednie lepkości w mm2/s. Dlatego wzór na wskaźnik lepkości został zmodyfikowany o poprawkę P wynikającą z przeliczenia lepkości na mm² i temperatury na °C. Zatem
|
WL = |
L - U L - H |
• 100 + P
| (6.51)
|
gdzie: L - lepkość kinematyczna w mm²/s oleju wzorcowego serii L w temperaturze 50°C (olej ten ma w 100°C taką samą lepkość jak olej badany), H - lepkość kinematyczna w mm²/s oleju wzorcowego serii H w temperaturze 50°C (olej ten ma w 100°C taką samą lepkość jak olej badany), U - lepkość kinematyczna w mm²/s oleju badanego w temperaturze 50°C.
Graficzne przedstawienie wyznaczania WL w układzie temperatura - lepkość przedstawiono na rys. 6.22b.
Należy zaznaczyć, że mogą istnieć oleje, w których zmiany lepkości są mniejsze niż olejów serii H. Mają one wskaźniki lepkości wyższe niż 100. Oleje wykazujące większe zmiany lepkości niż oleje serii L mają wskaźniki lepkości ujemne. Praktycznie w celu wyznaczenia wskaźnika lepkości badanego oleju konieczne jest zmierzenie lepkości badanego oleju w temperaturze 50°C i 100°C. Pozostałe dane odnoszące się do olejów wzorcowych bierze się z tablic. Często przy szybkim obliczaniu wskaźnika lepkości posługujemy się wykresami i nomogramami. Znając lepkość oleju w temperaturze 50°C i 100°C w °E lub mm²/s, można bez trudu z takich nomogramów odczytać wskaźnik lepkości.
Stosowanie wskaźnika lepkości jest bardzo wygodne, ponieważ za pomocą jednej liczby uzyskuje się charakterystykę zmian lepkości oleju wraz ze zmianami temperatury. Im wyższa wartość wskaźnika lepkości WL, tym lepkość oleju jest mniej wrażliwa na zmiany temperatury. Wskaźnik lepkości jest więc ważnym kryterium oceny przydatności eksploatacyjnej olejów. Jest on zależny od wielu czynników, a przede wszystkim od składu chemicznego oleju, a więc pośrednio i od pochodzenia oraz sposobu przeróbki ropy naftowej.
Najmniejszymi zmianami lepkości wraz ze zmianami temperatury charakteryzują się związki parafinowe. Rozgałęzienie łańcucha zmniejsza wartość wskaźnika lepkości. Dla węglowodorów cyklicznych, tj. naftenowych i aromatycznych, wartość wskaźnika lepkości maleje wraz ze wzrostem ilości pierścieni w cząsteczce, a rośnie i to bardzo silnie, wraz z ilością bocznych łańcuchów parafinowych. Rozgałęzienie bocznych łańcuchów wpływa na obniżenie wartości wskaźnika lepkości.
Węglowodory składające się z samych pierścieni aromatycznych lub mieszanych mają bardzo małe wartości wskaźnika lepkości. Najmniejsze jednak jego wartości mają związki asfaltowo-źywiczne. Ogólnie rzecz biorąc, ze względu na własności lepkościowe, najbardziej pożądanym składnikiem olejów są węglowodory parafinowe oraz węglowodory aromatyczne i naftenowe z długimi bocznymi łańcuchami parafinowymi.
Natomiast niepożądanymi składnikami są węglowodory aromatyczne i aromatyczno-naftenowe o skondensowanych pierścieniach, a przede wszystkim związki asfaltowo-źywiczne.
Najmniejsze wartości wskaźnika lepkości mają oleje z rop asfaltowych, a więc o dużej zawartości węglowodorów aromatycznych i aromatyczno-naftenowych.
Największe wartości wskaźnika lepkości mają oleje z rop parafinowych (a więc o dużej zawartości węglowodorów parafinowych lub bocznych łańcuchów parafinowych) oraz oleje syntetyczne.
Z procesów technologicznych największy wpływ na wskaźnik lepkości ma rafinacja. Największymi wartościami wskaźnika lepkości odznaczają się oleje rafinowane selektywnymi rozpuszczalnikami.
Znaczenie wskaźnika lepkości z punktu widzenia teoretycznego, jak również praktycznego, ograniczone jest przez to, że zależność lepkości od tempera- tury podaje się w wąskich przedziałach (50- 100°C). Nie może więc on charakteryzować zachowania olejów w warunkach temperatury znacznie odbiegających od temperatury pomiaru lepkości.
6.2.6. Zależność lepkości olejów od ich budowy chemicznej
Lepkość, podobnie jak inne własności fizyczne cieczy, zależy od jej budowy chemicznej. Im większe cząsteczki składają się na ciecz, tym większe są oddziaływania międzycząsteczkowe, a więc większe siły kohezji i większa lepkość. Ciecz składająca się z dużych cząsteczek ma wysoką temperaturę wrzenia. Dlatego też między temperaturą wrzenia a lepkością występuje zależność powiązana za pośrednictwem masy cząsteczkowej. Zależność między masą cząsteczkową a lepkością wykorzystuje się do określania średniej masy cząsteczkowej cząsteczek polimerów przez pomiar lepkości. Na lepkość ma bezpośredni wpływ nie tylko wielkość cząsteczek, ale również to, z jakich atomów są one zbudowane i jak wygląda ich przestrzenne rozmieszczenie w cząsteczce. Zwiększenie rozgałęzienia cząsteczek prowadzi z reguły do zwiększenia lepkości, gdyż przy wzajemnym przemieszczaniu się, cząsteczki zaczepiają się rozgałęzieniami, które działają tu jak przestrzenne przeszkody.
Spośród trzech grup węglowodorowych, z których składają się oleje z ropy naftowej, najmniejszą lepkością odznaczają się węglowodory parafinowe. Ich lepkość zwiększa się z długością łańcucha i ze stopniem jego rozgałęzienia.
Z dwóch pozostałych grup węglowodorowych, nafteny o małych cząsteczkach mają większe lepkości niż węglowodory aromatyczne o małych cząsteczkach. Dla wielopierścieniowych naftenów i aromatów zachodzi odwrotny stosunek, gdyż wpływ kondensowanych pierścieni aromatycznych jest tu większy niż wpływ kondensowanych pierścieni naftenowych.
Rozpatrywanie wpływu budowy przedstawicieli poszczególnych grup węglowodorowych na lepkość ma ograniczony charakter, gdyż występujących w olejach węglowodorów nie można zaliczyć do jednej z grup węglowodorowych, bowiem na ich budowę składają się elementy należące równocześnie do dwóch lub nawet trzech grup. Tak np. może być węglowodór o dwóch pierścieniach aromatycznych, jednym naftenowym, mający jeszcze ponadto boczne łańcuchy parafinowe.
Dlatego rozpatrując wpływ budowy na lepkość należy rozpatrywać wpływ poszczególnych elementów budowy. Prace w tym kierunku zapoczątkowane zostały przez Hugela, Lerera, Landę i Suidę.
Do poznania wpływu tych elementów w bardzo znacznym stopniu przyczyniły się badania Mikeski [33], Schieslera [41] oraz Piłata i jego żony [39].
Autorzy ci syntezowali odpowiednie węglowodory i przez „doczepianie” do nich różnych elementów badali ich wpływ na lepkość. Stwierdzili, że w przypadku węglowodorów parafinowych lepkość najintensywniej wzrasta przy wprowadzeniu pierścienia naftenowego sześciowęglowego, w mniejszym stopniu przy pięcioczłonowym, a w najmniejszym stopniu przy wprowadzeniu pierścienia aromatycznego (rys. 6.23).
Lepkość wzrasta wraz ze zbliżaniem się wprowadzonego pierścienia ku środkowi łańcucha. Tak więc alkilopochodne monocyklicznych naftenów mają wyższe lepkości od alkilopochodnych aromatycznych. Lepkość pochodnych alkilowych wzrasta wraz z długością łańcucha alkilowego oraz ze wzrostem liczby pierścieni w cząsteczce.
 |
Rys. 6.23. Zależność lepkości od liczby pierścieni w cząsteczce wg Czarnożukowa;
- - pochodne etylofenylowe,
- - pochodne propylocyklopentylowe,
- - pochodne etylocykloheksylowe
|
Tablica 6.4. Wpływ rodzaju pierścienia węglowodorowego C20 na lepkość (wg E. i St. Piłatów)
Węglowodór | Wzór strukturalny | Lepkość kinematyczna mm²/s |
w temperaturze 60°C | w temperaturze 98,9°C |
1-fenyloeikozan | 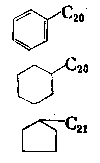 | 6,66 | 3,33 |
l -cykloheksyloeikozan | 8,40 | 4,13 |
l -cyklopentyloheneikozan | 7,88 | 3,80
| |
W tabl. 6.4 przedstawiono wpływ rodzaju pierścieni na lepkość, a w tabl. 6.5 - wpływ długości bocznych łańcuchów na lepkość.
Jak już wspomniano policykliczne węglowodory aromatyczne mają większą lepkość od policyklicznych naftenowych (tabl. 6.6). Tym też tłumaczy się wysoką lepkość związków asfaltowo-żywicznych.
Tablica 6.5. Wpływ długości bocznych łańcuchów węglowodorowych na lepkość (wg E. i St. Piłatów)
Węglowodór | Lepkość kinematyczna mm²/s |
w temperaturze 37,8°C | w temperaturze 98,9°C |
C10H7—C6H13 | 5,05 | 1,50 |
C10H7—C18H37 | 22,86 | 5,04 |
C10H7—C22H45 | 35,48 | 6,41
| |
Tablica 6.6. Wpływ rodzaju pierścieni na lepkość (wg E. Piłatowej)
Węglowodór | Lepkość kinematyczna mm²/s |
w temperaturze 37,8°C | w temperaturze 98,9°C |
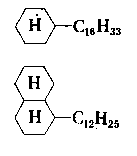 | 7,20 | - |
10,40 | 3,39 |
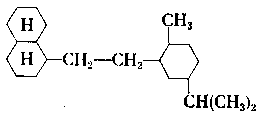 | 31,46 | 5,40 |
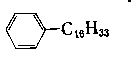 | 5,66 | - |
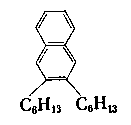 | 12,2 | 3,33
| |
Przy węglowodorach policyklicznych lepkość bardzo intensywnie podwyższają boczne łańcuchy parafinowe. Ich efektywność jest tym większa, im większa jest liczba łańcuchów (tabl. 6.7), im są one dłuższe (tabl. 6.5) i im bardziej rozgałęzione (tabl. 6.8 i 6.9).
Tablica 6.7. Wpływ liczby bocznych łańcuchów na lepkość (wg E. i St. Piłatów)
Węglowodór | Lepkość kinematyczna mm²/s |
w temperaturze 38,8°C | w temperaturze 98,9°C | | |
C6H5—C18H37 | 7,80 | 3,15 |
C6H4—(C18H37)2 | 48,80 | 9,82 |
C6H3—(C18H37)3 | 96,20 | 14,90 |
|
C10H7—C6H13 | 5,20 | 2,00 |
C10H6—(C6H13)2 | 19,50 | 4,03 |
C10H5—(C6H13)3 | 34,00 | 5,60
| |
6.2.7. Lepkość mieszanin
Lepkość nie jest wielkością addytywną. Zmieszanie ze sobą dwóch cieczy znacznie różniących się między sobą budową chemiczną powoduje znaczne odchylenia w stosunku do zależności prostoliniowej. Wszelkie przyczyny powodujące utrudnianie przemieszczania cząsteczek względem siebie, powodują zwiększenie lepkości.
Tablica 6.8. Lepkość rozgałęzionych węglowodorów parafinowych C26 w temperaturze 38°C (wg Cosly i Sutherlanda)
Węglowodór | Wzór strukturalny | Lepkość w temperaturze 37,8°C mm²/s | Temperatura krzepnięcia °C |
5-n-butylodokozan | | 11,48 | 20,8 |
5,14-dwu-n-butylo-okta-dekan | | 12,8 | 5,7 |
7-n-heksyloeikozan | | 10,69 | 10,2 |
3-etylo-5(2-etylo-butylo)okta-dekan | C2—C—C—C—C13 | | │ C2 | | │ C │ C—C2 │ C2 |
| - | -
| |
Odwrotnie, jeżeli domieszanie drugiej cieczy ułatwia poślizg, lepkość mieszaniny jest mniejsza w porównaniu z cieczą wyjściową. W praktyce trybologicznej bardzo często konieczne jest mieszanie ze sobą dwóch olejów dla uzyskania mieszaniny o żądanych własnościach lepkościowych. Mieszanie ze sobą olejów jest dopuszczalne w tym przypadku, gdy nie zawierają one dodatków (np. bazy olejowe lub oleje typu regular), bowiem przy mieszaniu olejów z dodatkami zachodzi obawa oddziaływania
Tablica 6.9. Lepkości rozgałęzionych węglowodorów parafinowych C26 w temperaturze 100° C (zestawienie na podstawie tablic Obolencewa)
Węglowodór | Wzór strukturalny | Lepkość w temperaturze 100°C mm²/s | Temperatura krzepnięcia °C |
n-heksakozan | CH3—(CH2)21—CH3 | 3,26 | 56,2 |
5-butylodokozan | | CH3 │ (CH2)3 │ | CH3—(CH2)3—CH—(CH2)16—CH3 |
| 2,98 | 20,8 |
11-pentylo-heneikozan | CH3—CH2—CH—CH2—CH3 | | │ | CH3—(CH2)9—CH—(CH2)9—CH3 |
| 2,73 | -40 |
| |
chemicznego dodatków ze sobą z wytworzeniem związków o niekorzystnym lub wręcz agresywnym działaniu. W celu uzyskania oleju o żądanej lepkości poprzez zmieszanie ze sobą olejów o dwóch różnych lepkościach, należy wiedzieć w jakim stosunku trzeba ją ze sobą zmieszać. Do obliczenia lepkości mieszaniny najlepiej nadaje się lepkościogram Molina-Gurwicza. Oparty jest on na wynikach pomiarów lepkości mieszanin dwóch olejów A i B, z których A miał lepkość E20 = 1,5°E, a B - E20 = 60°E. Skład mieszaniny był zmieniany w granicach od 0 do 100% obj. składnika A. Lepkościogram można stosować w następujący sposób. Chcąc znaleźć lepkość mieszaniny składającej się np. z 30% oleju o lepkości E20 = 12,5 i 70% oleju o lepkości E20 = 1,8 łączy się za pomocą prostej punkt 1,8 na skali B z punktem 72,5 na skali A (rys. 6.24). Z punktu odpowiadającego 30% składnika A
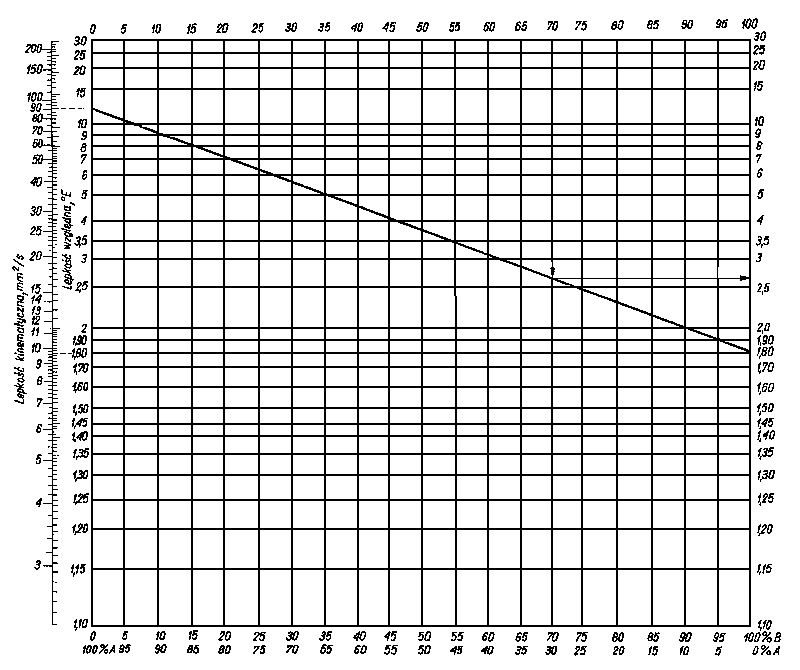 |
Rys. 6.24. Nomogram do wyznaczania lepkości mieszanin olejów
|
(70% składnika B) opuszcza się prostą pionową do przecięcia z poprzednią wyznaczoną prostą. Następnie z punktu przecięcia obu prostych prowadzi się prostą równoległą do osi odciętych aż do przecięcia z osią rzędnych, na której odczytuje się poszukiwaną lepkość mieszaniny.
6.2.8. Lepkość emulsji i zawiesin
Emulsjami nazywa się układy dwóch nie mieszających się ze sobą cieczy, z których jedna jest rozproszona (rozdrobniona) w drugiej pod postacią kropelek. Warunek wzajemnej nierozpuszczalności cieczy ma podstawowe znaczenie, gdyż przy zmieszaniu dwóch cieczy rozpuszczalnych w sobie otrzymuje się roztwór.
Zawiesinami nazywa się układy dwóch nierozpuszczalnych w sobie ciał, z których jedno jest cieczą zawieszającą (dyspergującą) drobne cząstki ciała stałego (ciało zdyspergowane).
Zarówno w przypadku emulsji, jak i zawiesin, zachodzi podobna sytuacja, tj. w cieczy mamy rozdrobnione cząstki obcego ciała, którym mogą być kropelki drugiej cieczy lub cząstki ciała stałego. Pod działaniem sił ścinających następuje przemieszczanie się cieczy dyspergującej względem ciała zdyspergowanego. Tak więc oprócz tarcia wewnętrznego cieczy, mamy do czynienia z tarciem zewnętrznym na granicy rozdziału faz (rys. 6.25).
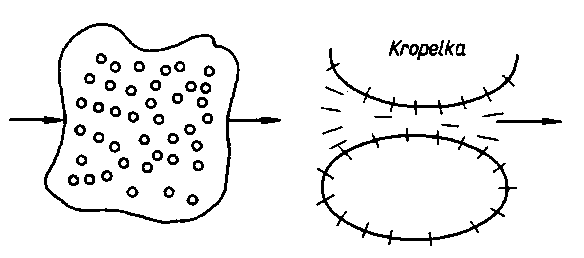 |
Rys. 6.25. Model tarcia na granicy faz emulsji
|
Ze względu na to, że powierzchnie rzeczywistego kontaktu są bardzo duże, a więc i działające siły między cząsteczkowe, adhezyjne są duże, lepkość wzrasta bardzo znacznie. Przykładem mogą być różnego rodzaju majonezy (emulsja żółtka w oleju roślinnym), emulsje olejów mineralnych z wodą.
W przypadku zawiesin obecność cząstek ciała stałego w cieczy powoduje dodatkowo nadawanie cieczy charakteru cieczy nienewtonowskiej, z czym wiążą się różnego rodzaju anomalie lepkości.
6.2.9. Lepkość olejów zapowietrzonych
W układach olejenia wielu maszyn olej zemulgowuje stykające się z nim powietrze, tworząc z nim układ, w którym fazą zdyspergowaną jest powietrze, a fazą dyspergującą olej. Pozornie wydawać by się mogło, że wprowadzenie do oleju czynnika, którego lepkość jest znikoma, spowoduje zmniejszenie lepkości emulsji olejowo-powietrznej. Jednakże podobnie, jak w przypadku emulsji dwóch cieczy, tak i przy wprowadzeniu do oleju powietrza, lepkość emulsji olejowo-powietrznej ma nieco większą wartość niż oleju niezapowietrzonego.
Einstein [1] rozpatrywał problem lepkości ośrodka, w którym znajdują się kuliste cząstki ciała sztywnego całkowicie zwilżone cieczą dyspergującą. Doszedł do wniosku, że stosunek lepkości cieczy z zawiesiną hz do cieczy czystej ho wynosi
|
hz ho |
= 1 + 0,025 b
| (6.52)
|
gdzie: b - procentowy (obj.) udział fazy rozproszonej.
Problem ten był rozpatrywany również przez Taylora [1], który założył, że rozproszone ciało jest cieczą o lepkości h`. Otrzymał on wzór na stosunek hz/ho
|
hz ho |
= 1 + 0,025 b |
h` + 0,4 ho h` + ho
| (6.53)
|
Jeżeli założy się, że zdyspergowane ciało jest nielepkie, to wyrażenie ułamkowe zbliża się do wartości 0,4, a całe równanie Taylora przybiera postać
|
hz ho |
= 1 + 0,010 b
| (6.54)
|
Hayward [l] przeprowadził eksperymentalną weryfikację powyższych wzorów. Stosując specjalny lepkościomierz zmierzył lepkość olejów zapowietrzonych (do 25% powietrza) typu regular i olejów z dodatkami. Wartość „b” wyznaczył przez pozostawienie oleju w spokoju, co pozwalało na stopniowe wydzielenie się powietrza. Ustalił on empiryczną zależność
|
hz ho |
= 1 + 0,015 b
| (6.55)
|
Stwierdził, że wpływ zapowietrzenia na lepkość olejów jest niewielki zarówno dla olejów z dodatkami, jak i olejów typu regular. Podany powyżej wzór ma zastosowanie do olejów o małych i dużych lepkościach. Jest on również słuszny w przypadku, gdy rozdrobnienie jest bardzo duże, jak i w przypadku, gdy banieczki powietrza są stosunkowo duże.
6.2.10. Dodatki zwiększające lepkość i wskaźnik lepkości oleju (wiskozatory)
6.2.10.1. Mechanizm działania
Istnieje wiele urządzeń, które ze względu na warunki w obszarach tarcia (wysoka temperatura, wysokie naciski jednostkowe itp.) muszą być smarowane olejami o dużej lepkości. Nie we wszystkich jednak ropach występują węglowodory o dużych lepkościach. Z wielu gatunków rop można otrzymać olej jedynie o małych i średnich lepkościach. W wielu ropach występują ciężkie frakcje olejowe, trudno je jednak uwolnić od towarzyszących im w bardzo dużej ilości związków asfaltowo-żywicznych, dlatego też proces otrzymywania ciężkich frakcji olejowych może być drogi, a czasami nieopłacalny.
W przypadku produkcji olejów smarowych z rop nie mających ciężkich frakcji olejowych konieczne jest nieraz zwiększenie lepkości olejów o małej i średniej lepkości przez wprowadzanie dodatków. Ma to szczególne znaczenie, gdy w danym kraju przerabia się tylko jeden typ ropy, a więc gdy braki w ciężkich frakcjach oleju nie mogą być uzupełniane olejami z przeróbki innych rodzajów ropy.
Bardzo często zwiększanie lepkości frakcji oleju uzyskuje się przez zmieszanie jej z brightstockiem - olejem pozostałościowym o charakterze parafinowo-naftenowym o bardzo dużej lepkości (n50 ≈ 300 mm²/s). Brightstock można otrzymać tylko z pewnych gatunków ropy przez odasfaltowanie propanowe, dlatego w wielu krajach brightstock pochodzi z importu.
Innym sposobem zwiększenia lepkości olejów jest wprowadzenie do nich związków o znacznej masie cząsteczkowej. Zazwyczaj są to ciekłe polimery. Dodatki podwyższające lepkość zwykle zwiększają również wskaźnik lepkości WL, a bardzo często polepszają zachowanie się oleju w niskiej temperaturze. Wydawać by się mogło, że stosowanie dodatków podwyższających lepkość jest doskonałym sposobem otrzymywania olejów o dużych lepkościach.
W wielu przypadkach stosowanie takich dodatków może być bardzo niebezpieczne. Tak np. w silniku istnieją warunki do częściowego odparowania składników oleju. Intensywność odparowania jest zazwyczaj większa u olejów o mniejszej lepkości, gdyż mają one niższą temperaturę wrzenia. Przy olejach zagęszczonych dodatkami, olej częściowo odparowuje pozostawiając zagęszczacz, co może spowodować zaklejenie lub zakoksowanie współpracujących elementów. Z tych względów ogranicza się zawartość zagęszczaczy do 1÷ 2% dla olejów lotniczych i 6 ÷ 8% dla olejów samochodowych.
Mechanizm podwyższenia lepkości przez dodatki zagęszczające oraz zmniejszenie zmian lepkości wraz ze zmianami temperatury nie jest jeszcze całkowicie wyjaśniony. Wielu autorów wraz ze Staudingerem - badaczem układów wielkocząsteczkowych uważa, że wprowadzenie do rozpuszczalnika o małej lepkości (w naszym przypadku oleju) cząsteczek polimeru o długiej nitkowatej budowie, silnie hamuje ruchy cząsteczek rozpuszczalnika, a więc zwiększa jego lepkość. Cząsteczka polimeru o takiej budowie ze względu na swą znaczną długość styka się z wieloma cząsteczkami rozpuszczalnika i oddzialywuje na nie siłami międzycząsteczkowymi. W ten sposób każda cząsteczka polimeru potrafi ,,unieruchomić" wiele cząsteczek rozpuszczalnika, a więc mała ilość dodatku potrafi silnie zwiększyć lepkość.
Niektórzy uważają, że długie nitkowate cząsteczki polimeru zginają się i tworzą kłębki. Wzrost temperatury powoduje rozwijanie się (pęcznienie) kłębka. Hamuje to obniżanie lepkości w podwyższonej temperaturze.
Wprowadzenie dodatków zagęszczających często powoduje zmianę charakteru cieczy z newtonowskiej na nienewtonowską.
6.2.10.2. Rodzaje dodatków
Dodatki zagęszczające zwane są często wiskozatorami. Zazwyczaj są to różnego rodzaju wielkocząsteczkowe polimery. Ostatnio największe zastosowanie znalazły jako ciekłe polimery dodawane do olejów poliakrylany, polimetakrylany oraz poliizobutyleny.
Rzadziej stosowane są różnego rodzaju kopolimery styrenu z olefinami, polimery kwasu fumarowego, polimery eteru winylowo-butylowego i woltole. Poliizobutyleny dla celów zagęszczania olejów dają najlepsze efekty, gdy mają masę cząsteczkową 10000-15000. Niemniej jednak, stosowane są również poliizobutyleny o mniejszych i większych masach cząsteczkowych.
|
Wiskozatory poliizobutylenowe mają różne handlowe nazwy Superol (ZSRR), Oppanol (firma BASF- RFN), Paraton i Exanol (firma Standard Oil - USA).
Polimetakrylany i poliakrylany wprowadzane do olejów mają zazwyczaj masy cząsteczkowe 10 000 - 20 000.
|
gdzie: R-grupy alkilowe wprowadzane podczas estryfikacji kwasu metakrylowego różnymi alkoholami.
|
Dodatki polimetakrylanowe i akrylanowe również mają różne nazwy handlowe: Montovis (firma Monsanto), Viscoplex i Plexol (RFN), Acryloids (USA), Vindex (Węgry), Glisoviscal, Garbacryl, Empicryl i inne.
Rzadziej są stosowane dodatki polistyrenowe o masie cząsteczkowej 10000-20000.
|
Mają one handlowe nazwy, np. Santodex (firma Monsanto). Ostatnio stosowane są również w niektórych krajach polimery kwasu fumarowego (kwasu trans-eteno-dwukarboksylowego COOHCH═CHCOOH).
Polimery eteru winylo-n-butylowego są stosowane głównie w Związku Radzieckim pod nazwą Winipolu.
Woltole są to produkty otrzymywane z olejów roślinnych lub mieszanin olejów roślinnych z mineralnymi, pod działaniem cichych wyładowań elektrycznych (200-3000 okresów/s przy napięciu 2000-20000 V), w atmosferze gazu obojętnego. Olej poddawany wyładowaniom w cienkich warstwach ogromnie zwiększa swoją lepkość, gdyż wyładowania powodują kondensację i polimeryzację cząsteczek.
Bardzo poważną wadą zagęszczaczy jest ich mała odporność na oddziaływanie mechaniczne i działanie wysokiej temperatury. W wyniku oddziaływań mechanicznych, polimery ulegają degradacji (zmniejszenie masy cząsteczkowej), co powoduje zmniejszenie lepkości w czasie eksploatacji, a więc zaburzenia w procesie smarowania. Przy smarowaniu elementów pracujących w stosunkowo wysokiej temperaturze polimery mogą ulegać rozkładowi termicznemu połączonemu z zakoksowaniem powierzchni.
6.2.10.3. Mechaniczna degradacja dodatków polimerowych (ścinanie polimerów)
Oleje, których lepkość została zwiększona przez wprowadzenie polimerów, zmniejszają swoją lepkość podczas pracy w urządzeniach. Stwierdzono, że przyczyną zmniejszenia lepkości jest zmniejszenie masy cząsteczkowej wprowadzonych polimerów. Zjawisko to jest określane nazwą ścinania lub mechanicznej degradacji polimerów (rys. 6.26a). Występuje ono przy dużych prędkościach ścinania podczas tarcia przy
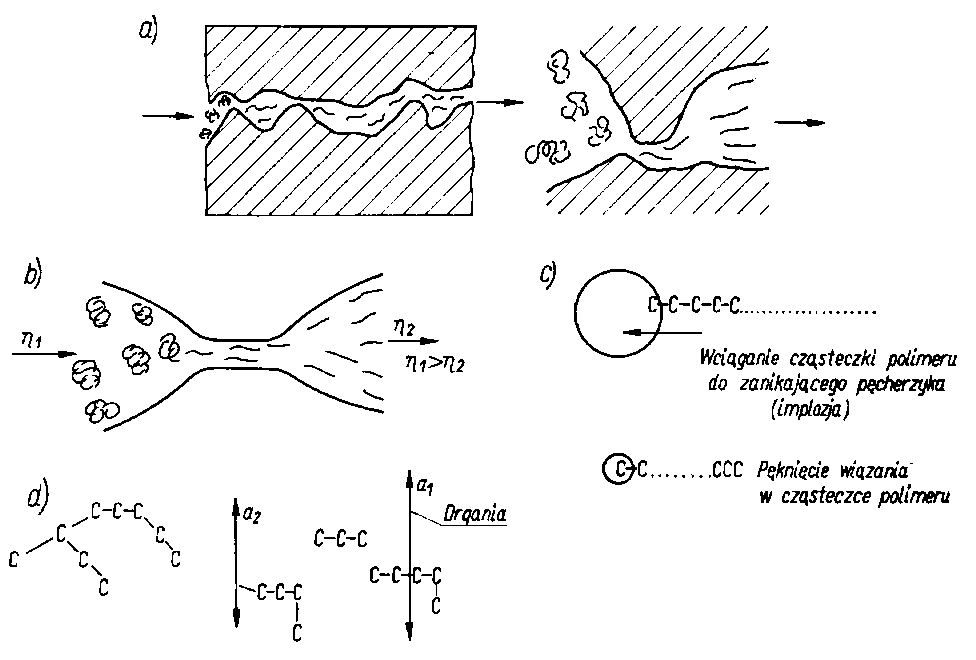 |
Rys. 6.26. Degradacja-ścinanie polimerów (wg Wiślickiego):
- degradacja-przez tarcie, ścinanie mechaniczne,
- degradacja przez dławienie,
- degradacja kawitacyjna,
- degradacja w polu akustycznym;
a = amplituda drgań
|
wysokich naciskach jednostkowych, podczas przeciskania cieczy przez szczeliny, podczas kawitacji, przy działaniu fal ultradźwiękowych itd. Pomimo, że wymienione oddziaływania mechaniczne powodują zmniejszanie masy cząsteczkowej istnieją również poglądy, że bezpośrednią przyczyną rozrywania łańcuchów polimerów jest energia cieplna, powstała w mikroobszarach styku na skutek oddziaływania mechanicznego (miażdżenia, ucierania lub ugniatania cieczy roboczej). Niezależnie od tego czy degradacja zachodzi bezpośrednio pod działaniem sił ścinających, czy też poprzez oddziaływanie cieplne, ważny jest negatywny efekt obniżenia lepkości.
Degradacja polimerów poprzez działanie fal ultradźwiękowych ma zasadnicze znaczenie w badaniach odporności na ścinanie olejów zagęszczonych, gdyż stanowi najszybszy sposób obniżenia masy cząsteczkowej zagęszczaczy. Działanie fal ultradźwiękowych o odpowiednio wielkich amplitudach powoduje rozrywanie cząsteczek. Wielkie nitkowate, poplątane cząsteczki polimerów o dużej bezwładności nie nadążają za ruchami drgającymi rozpuszczalnika, a powstające w ten sposób siły tarcia są wystarczające do zerwania wiązań między atomami w cząsteczce.
Dodatkowo podczas działania fal ultradźwiękowych mamy zazwyczaj do czynienia z kawitacją. Przy rozchodzeniu się fal ultradźwiękowych powstają kolejno po sobie zagęszczenia i rozrzedzenia cieczy, prowadzące do tworzenia się i zanikania pęcherzyków kawitacyjnych. Czas życia pęcherzyka kawitacyjnego jest rzędu kilkudziesięciu mikrosekund. Przy jego tworzeniu i zanikaniu (implozja) cząsteczki najmniej ruchliwe, a więc cząsteczki polimeru, podlegają działaniu gwałtownych sił rozrywających. W otoczeniu pęcherzyka wzrasta również temperatura powodując dodatkowy efekt destrukcyjny. W maszynach i urządzeniach mamy w wielu przypadkach do czynienia ze zjawiskami kawitacyjnymi w układach olejenia (odrywania się cieczy smarnej od powierzchni, zawirowywania w czasie przepływu, gwałtowne gradienty ciśnienia w strukturze itp.) prowadzącymi do mechanicznej degradacji polimerów.
6.2.10.4. Metody badania odporności olejów na ścinanie
Wprowadzanie polimerów (wiskozatorów) do olejów ma na celu zwiększenie lepkości do wartości wymaganej w danym urządzeniu. Jeżeli w wyniku ścinania polimeru lepkość oleju obniża się, to wówczas olej zostaje zdyskwalifikowany jako ciecz smarująca do danego urządzenia. Jednym z podstawowych kryteriów oceny przydatności eksploatacyjnej olejów z polimerami jest określenie ich odporności na ścinanie. Badanie tego rodzaju możemy prowadzić w warunkach eksploatacyjnych lub w warunkach laboratoryjnych.
Badania laboratoryjne mogą mieć na celu albo odwzorowanie warunków eksploatacyjnych (badania takie trwają zazwyczaj bardzo długo), albo zrealizowanie ścinania w możliwie krótkim czasie dla uzyskania szybkich informacji o przydatności oleju.
W celu określania odporności olejów na ścinanie stosuje się najczęściej następujące urządzenia:
1) Urządzenia typu pompa-szczelina. W urządzeniach tych olej zazwyczaj jest tłoczony w obiegu zamkniętym przez pompę zębatą, tłoczkową lub łopatkową. Rolę szczeliny spełnia zawór ciśnieniowy, wtryskiwacz silnika wysokoprężnego lub element o większej liczbie otworów.
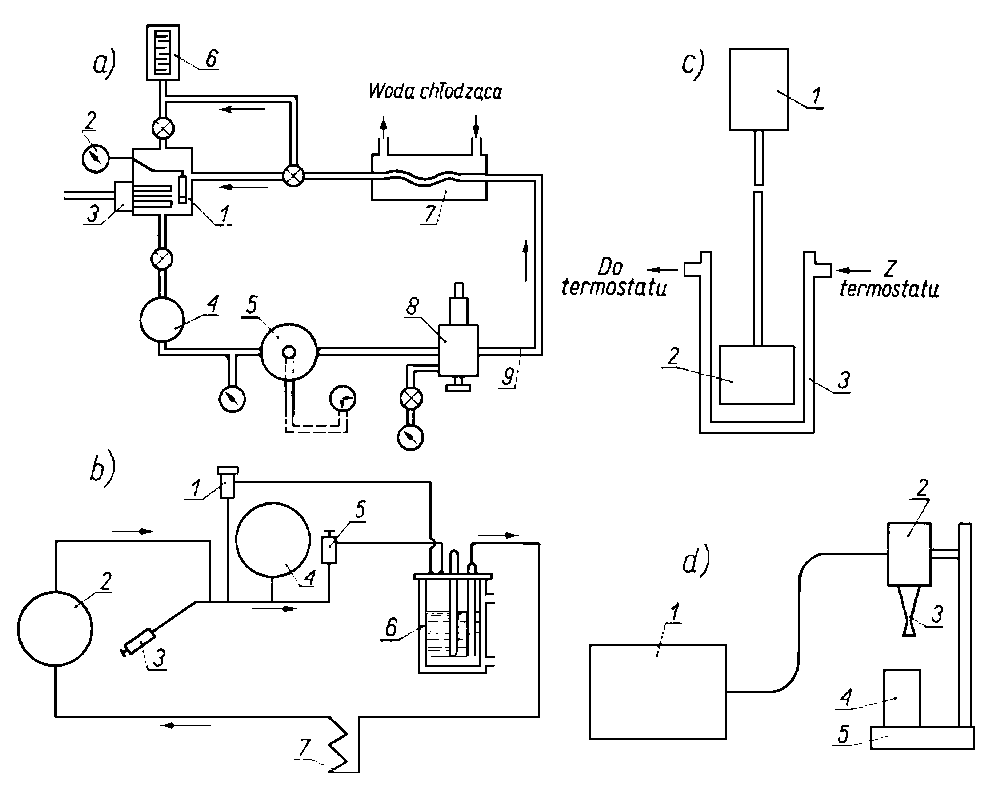 |
Rys. 6.27. Schematy urządzeń do mechanicznego ścinania olejów:
a) urządzenie typu pompa-szczelina:
- - zbiornik główny,
- - termometr,
- - grzejnik nurkowy,
- - filtr,
- - pompa,
- - naczynie pomiarowe,
- - naczynie chłodzone,
- - zawór,
- - dławienie labiryntowe;
|
b) urządzenie typu pompa-szczelina:
- - zawór bezpieczeństwa,
- - pompa,
- - zawór spustowy,
- - manometr,
- - zawór dławiący,
- - zbiornik oleju,
- - chłodnica;
|
c) mieszadło ścinające:
- - silnik elektryczny napędzający,
- - mieszadło,
- - naczynie pomiarowe;
|
d) promiennik ultradźwięków:
- - generator,
- - przetwornik
- - sonotroda,
- - naczyńko na ciecz,
- - statyw
| |
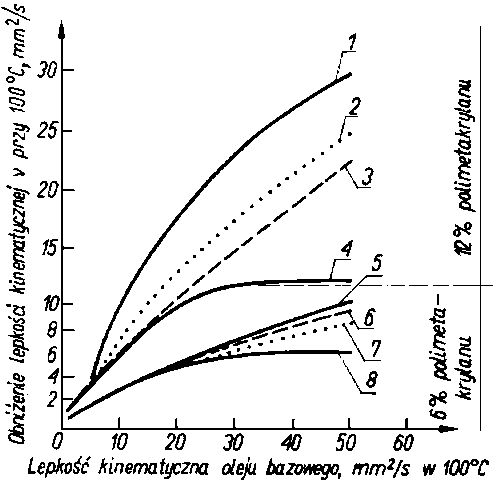 |
Rys. 6.28. Odporność polimerów na ścinanie przy badaniu różnymi metodami olejów różniących się lepkościami (wg Rossa);
- - badania eksploatacyjne (przekładnia),
- - maszyna FZG (po 7 godzinach),
- - wtryskiwacz,
- - aparat ultradźwiękowy,
- - badania eksploatacyjne,
- - maszyna FZG (po 7 godzinach),
- - wtryskiwacz,
- - aparat ultradźwiękowy
|
Przykładowe urządzenia tego rodzaju przedstawione są na rys. 6.27, Znaczny efekt ścinania uzyskuje się już po kilku cyklach przejścia oleju przez szczelinę (wtryskiwacz) (rys. 6.28).
2) Urządzenia do badania kół zębatych (np. maszyna FZG), w których zagęszczacz polimerowy jest degradowany podczas współpracy zębów dwóch kół zębatych.
3) Urządzenia ultradźwiękowe (generatory ultradźwiękowe). Intensywność ścinania zależy od mocy generatora ultradźwięków, częstotliwości drgań, profilu elementu wysyłającego drgania (koncentratora) itp. Badania za pomocą urządzeń ultradźwiękowych mają tę zaletę, że wymagają małej ilości cieczy do badań (kilka do kilkudziesięciu cm³) i dają już po krótkim czasie znaczny efekt ścinania (zazwyczaj kilkanaście minut).
4) Szybkoobrotowe mieszadła, homogenizatory, lepkościomierze rotacyjne itp. W urządzeniach tych znaczniejsze efekty ścinania uzyskuje się dopiero przy dużej prędkości obrotowej (ok. 20 000 obr/min).
Do badań laboratoryjnych można zaliczyć również badania odporności oleju na ścinanie prowadzone z wykorzystaniem silnika spalinowego zamontowanego na stanowisku hamownianym. Badania te są długotrwałe i drogie (obsługa silnika, koszt paliwa itp.)
Badania eksploatacyjne są prowadzone podczas normalnej eksploatacji samochodów. Wyniki badań eksploatacyjnych i hamownianych są obarczone błędem wynikającym z obniżenia lepkości wskutek rozcieńczenia oleju niespalonym paliwem. Aby ten błąd wyeliminować niejednokrotnie badania prowadzi się wykorzystując samochody napędzane płynnym gazem.
3 obiegi przez aparaturę wtryskową,
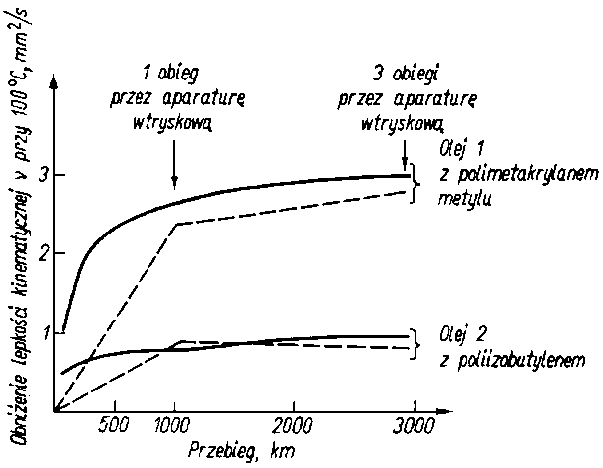 |
Rys. 6.29. Wyniki badań odporności na ścinanie olejów zagęszczonych polimerami; linia ciągła - badania eksploatacyjne, linia przerywana - badania na aparacie wtryskowym
|
Porównanie efektów ścinania uzyskiwanych za pomocą różnych urządzeń przedstawiono na rys. 6.28 i 6.29. W przypadku olejów o zawartości 6% polimeru otrzymuje się bardzo zbliżone efekty ścinania przy badaniach eksploatacyjnych samochodowych i badaniach za pomocą aparatury wtryskowej silnika wysokoprężnego. Badania przeprowadzone w przypadku olejów o większej zawartości polimeru (12%) dają większą rozbieżność pomiędzy poszczególnymi metodami badań.
Ocenę odporności oleju na ścinania (ONS) prowadzi się opierając się na obniżeniu lepkości obliczanej ze wzoru
|
ONS = | lepkość oleju świeżego - lepkość oleju po ścinaniu lepkość oleju świeżego
|
• 100
|
(W literaturze anglosaskiej ONS oznacza się skrótem SSI - Shear Stability Index).
Wyraża się również odporność na ścinanie odniesioną do polimeru ONSpol
|
ONSpol = |
lepkość oleju świeżego - lepkość oleju po ścinaniu lepkość oleju świeżego - lepkość oleju bez polimeru |
• 100
|
W literaturze anglosaskiej jest również stosowane pojęcie lepkościowej efektywności polimeru
|
Lepkościowa efektywność polimeru = 100 - ONSpol
|
Autorzy książki wprowadzili inny sposób oceny intensywności ścinania polegający na wydzielaniu zdegradowanego polimeru z oleju i określaniu jego masy cząsteczkowej. W ten sposób można uzyskać znacznie więcej informacji o wpływie warunków eksploatacyjnych na odporność polimeru na ścinanie niż z obniżenia lepkości.
6.2.10.5. Wpływ budowy chemicznej dodatku polimerowego na jego odporność na ścinanie
Intensywność degradacji dodatku polimerowego zależy od tego, co podlega ścinaniu i w jakich warunkach. Na warunki ścinania składają się: temperatura, czas, wartość naprężenia i prędkość ścinania. Wpływ tych czynników poglądowo przedstawiono na rys. 6.30 i 6.31. Spośród czynników chemicznych największą rolę spełniają: rodzaj poddawanego ścinaniu dodatku, jego stężenie w oleju i średnia masa cząsteczkowa, rozrzut wartości masy cząsteczkowej, budowa przestrzenna polimeru (długość cząsteczki, boczne łańcuchy itp.).
Dla polimerów stosowanych jako wiskozatory można ustalić następujące prawidłowości:
Wzrost efektywności w podwyższaniu wskaźnika lepkości i lepkości
| ↑ |
Poliakrylany
Polimetakrylany
Polifumarany
Poliizobutyleny
| ↓ |
Wzrost odporności na ścinanie
|
Im większa cząsteczka, a więc im większa masa cząsteczkowa, tym polimer łatwiej ulega ścinaniu. Dla każdego naprężenia ścinającego można ustalić „krytyczną" masę cząsteczkową, powyżej której odporność na ścinanie gwałtownie maleje. Zależność tą przedstawiono na rys. 6.30 d.
Jeżeli rozrzut wartości masy cząsteczkowej polimeru jest duży, wówczas efekt ścinania jest mniejszy niż w przypadku polimerów o jednorodnym składzie cząsteczkowym.
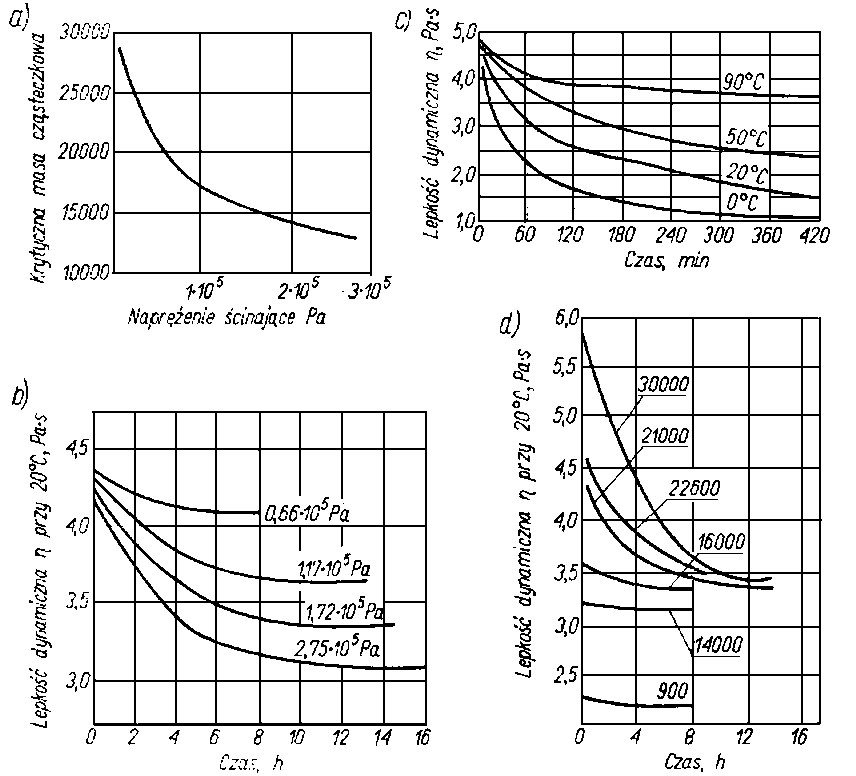 |
Rys. 6.30. Wpływ ścinania na zmiany lepkości oleju zagęszczonego polimerami (wg Siemienido):
- zależność krytycznej masy cząsteczkowej od wartości naprężenia ścinającego,
- zmiany lepkości roztworu w oleju, poliizobutylenu o masie cząsteczkowej 21000 przy różnych wartościach naprężenia ścinającego,
- zmiana lepkości 5-proc. roztworu poliizobutylenu. Mc = 30000 w oleju turbinowym przy ścinaniu w temperaturach 0, 20 i 90°C,
- zmiany lepkości 5% roztworu poliizobutylenu o różnej masie cząsteczkowej przy działaniu naprężenia ścinającego równego 0,172 Pa
|
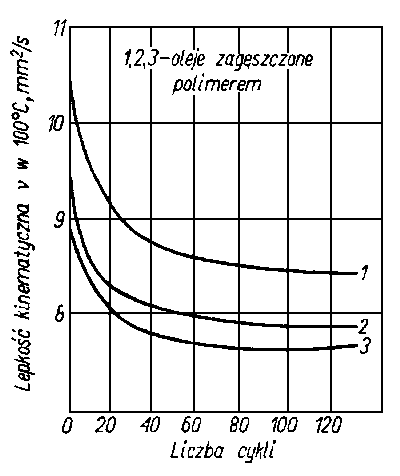 |
Rys. 6.31. Zależność lepkości od liczby cykli przy ścinaniu polimerów; 1,2,3-oleje zagęszczone polimerami
|
6.2.11. Eksploatacyjne znaczenie lepkości
Lepkość jest jedną z własności mających największe znaczenie w eksploatacyjnej przydatności oleju. Duża lepkość oleju wprowadzonego w skojarzenie tarciowe utrudnia wyciśnięcie go spomiędzy trących elementów, a więc zabezpiecza te elementy przed ich zatarciem. Duża lepkość, czyli duże opory tarcia wewnętrznego, powodują jednak znaczne straty mocy pracującego urządzenia. Tak więc dobór lepkości oleju musi uwzględniać dwa przeciwstawne dążenia, tj. dążenie do uzyskania trwałej warstwy oleju i dążenie do możliwie małych oporów tarcia skojarzenia. Przy doborze lepkości oleju do jakiegoś urządzenia, bierze się pod uwagę przede wszystkim warunki w jakich będzie on pracował, a więc temperaturę, obciążenie i jego zmiany w czasie oraz prędkość obrotową lub liniową.
Im wyższa temperatura i im wyższe obciążenie smarowanych skojarzeń, tym olej musi mieć większą lepkość. Natomiast im większa prędkość liniowa, tym mniejszą lepkość dobiera się ze względu na to, że przy dużej prędkości o wiele łatwiejsze jest utworzenie klina smarującego, a duża lepkość powoduje niepotrzebne straty mocy.
Do prawidłowej pracy urządzenia nie wystarcza tylko dobranie odpowiedniej lepkości, ale lepkość musi jak najmniej zmieniać się wraz ze zmianami temperatury, gdyż zazwyczaj temperatura wzrasta w czasie pracy urządzenia, co powoduje zmniejszenie lepkości.
Na skutek zmniejszania lepkości oleju wraz z podwyższeniem temperatury obniża się zazwyczaj ciśnienie w układzie olejenia. Może to powodować niedostateczny dopływ oleju do obszarów tarcia. Szczególnie niebezpieczne jest to w wysokich temperaturach.
W silnikach o złym stanie technicznym, wskutek zwiększenia luzów między współpracującymi częściami, trudniejsze jest uszczelnienie pierścieni tłokowych, uzyskanie odpowiednio grubej warstwy oleju w łożyskach itp. przy stosowaniu oleju o małej lepkości.
Przy obniżaniu temperatury, zwłaszcza w zimie, gdy lepkość oleju wzrasta, powstają trudności w uruchomieniu urządzenia, np. silnika.
Nadmierny wzrost lepkości oleju może poważnie utrudniać pracę pompy oleju, co wyraźnie wpływa na jej wydajność. Z tych wszystkich względów dobór oleju o odpowiednich własnościach lepkościowych ma bardzo poważne znaczenie.
W czasie pracy oleju w urządzeniach, lepkość oleju zmienia się. W wyniku procesów polimeryzacyjnych i kondensacyjnych oraz procesów utleniania, lepkość zwiększa się. W czasie pracy oleju w tłokowych' silnikach spalinowych, niespalone paliwo powoduje rozcieńczenie oleju i zmniejszenie jego lepkości. Zjawisko to jest szczególnie nasilone w okresie eksploatacji zimowej, natomiast w znacznie mniejszym stopniu obserwuje się go podczas eksploatacji w ciepłych porach roku. Zazwyczaj zmniejszenie lepkości w wyniku rozcieńczenia paliwem jest większe niż wzrost lepkości w wyniku procesów starzenia, co prowadzi ostatecznie do stopniowego zmniejszania się lepkości oleju w czasie pracy w silnikach. W urządzeniach, w których olej nie ulega rozcieńczeniu, procesy starzenia powodują stopniowy wzrost lepkości oleju.
|