|
Effects of Thermal Treatment and Sliding on Chemical Bonding of PFPE Lubricant Films with DLC Surfaces
Zheming Zhao,¹ Bharat Bhushan,¹ and Czeslaw Kajdas²
¹ Computer Microtribology and Contamination Laboratory, Department of Mechanical Engineering; The Ohio State University, Columbus, Ohio 43210-1107
² Warsaw University of Technology, Institute of Chemistry, Plock, and Central Laboratory of Petroleum in Warsaw, Poland
* — Published in : J. Info. Storage Proc. Syst, Vol., 1, 259-264, 1999
Abstract
The bonding characteristics of polar perfluoropoly(ether) (PFPE) lubricant Z-Dol and nonpolar PFPE lubricants Z-15 and Z-25 with diamondlike carbon (DLC) surfaces were studied. For lubricant Z-Dol, either prebaking the disk before lubrication or a paper pad's being slid on the lubricated disk was found to enhance the bonding capability of lubricant film on the surface of the magnetic disk with DLC coating. For nonpolar lubricants Z-15 and Z-25, a paper pad's sliding on the lubricated disk resulted in some bonding of lubricant molecules on the DLC disk surface. Experimental results were repeatable. The mechanisms of pre sliding responsible for lubricant bonding are discussed, based on the concept of the hydrogen bond interaction and low-energy electron emission, respectively.
1. INTRODUCTION
The liquid lubricants commonly used for thin-film disks are perfluoropoly(ether) (PFPE) lubricants available with or without functional end groups (Bhushan, 1996). Lubricants with —OH end groups are polar lubricants that can chemically bond to the lubricated surface. Attachment of the liquid lubricant molecules has to be enhanced to the overcoat, which, for most cases is sputtered diamondlike carbon (DLC). Surface cleanliness and chemical activity of the overcoat affect the degree of bonding.
In a previous study by Zhao and Bhushan (1996), the effects of soaking time (the period of time the disk was left in the lubricant-solvent mixture during lubrication), baking time, and temperature during postbake were studied as shown in Fig. 1. Disks (type A) were used with an rms roughness of 2.7 nm. In Fig. l (a), the bonded lubricant thickness increased with an increased soaking time for films unbaked (22 °C) and baked at 150 °C. The bonded thickness reached to near saturation after soaking for 15 min. At a fixed soaking time and baking temperature, the bonded lubricant thickness increased with an increased baking time; see Fig. l(b). Baking at 150 °C increased the bonded lubricant thickness as compared to baking at 100 °C and the unbaked sample; see Fig. l (c). The bonded lubricant thickness increased with an increasing, applied lubricant thickness and tended to saturate at the lubricant thickness of 8 nm. It should be noted that all of these thermal treatments were performed after the disk was lubricated.
Nevertheless, little is known about the attachment of PFPE lubricants to the surface and the role of the surface chemistry in the interface tribology. In this (to our knowledge) first-of-a-kind study, the effect of prebaking the disk surface to enhance the chemical bond for polar PFPE lubricant such as Z-Dol was studied. Also, the effect of sliding on the degree of the chemical bonding of nonpolar lubricants such as Z-15 and Z-25 was studied.
2. Experimental
The chemical molecular structures of lubricant used in the test are shown in Table 1. For thermal treatment,
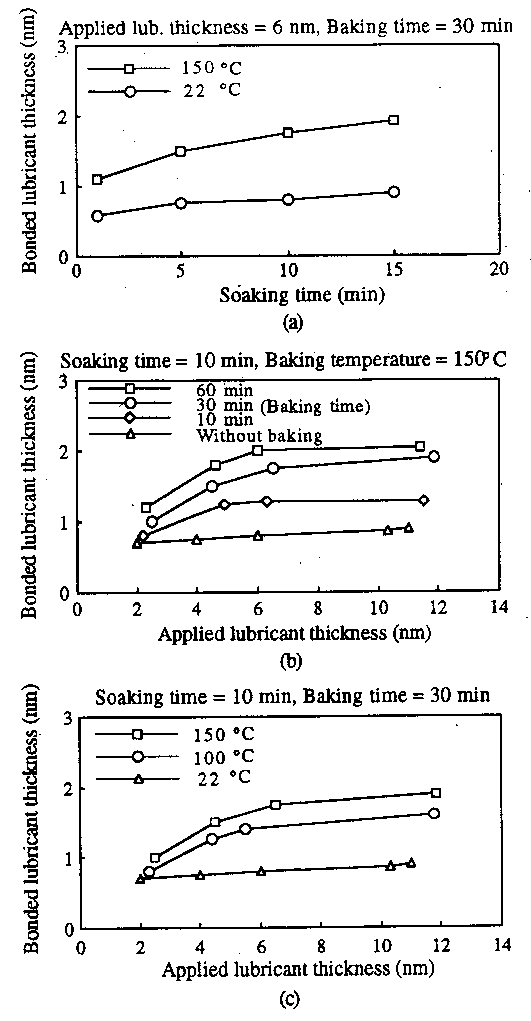 |
Fig. 1. Bonded lubricant film thickness as a function of
soaking time, and
(b) and (c) applied lubricant thickness, with the effects of baking temperature and time for postbaking.
|
unlubricated polished disks (type B) with an rms surface roughness of 0.5 nm were used. In each test, two disk coupons were taken from the same disk. One of them was prebaked at 150 °C for 2 h. The disk coupons were lubricated with Z-Dol. Lubricated disks were postbaked at 150 °C at various times. The disks were then washed with solvent FC-72. The bonded fraction of lubricant was measured by using ellipsometry (Zhao and Bhushan, 1996).
For the sliding effect study, a 70% size of head slider was used. The head slider (overall dimensions: 2.85 mm x 2.24 mm: rail length =2.59 mm: and rail width = 0.33 mm) was covered with a paper pad that was 3 mm x 2 mm in size and that had a surface rms roughness of 35 nm. Disks that were not prebaked were lubricated with various lubricants to various thicknesses, and no posttreatment was carried out. Sliding tests were conducted at 12 m/s. A normal load of 50 mN was used. After the sliding test, the disk surface was washed with solvent FC-72, and then bonded fraction of lubricant film was measured by using ellipsometry.
3. RESULTS AND DISCUSSION
3.1. Effect of Prebake
Table 2 shows the thickness of the bonded film of lubricant Z-Dol with or without prebaking at 150 °C. The prebaked disks produce a thicker chemically bonded lubricant film, by a factor of 2, compared to that of unbaked disks. For a same postbaking time of 30 min, an increase in the applied lubricant film thickness from 4.7 nm to 12 nm increases the bonded layer thickness from 0.8 nm to 1.0 nm. For the same applied film thickness of 12 nm, the bonded fraction increases from 1.0 nm to 1.2 nm with an increase in the postbaking time from 30 min to 60 min. For disks that were not prebaked, the bonded layer of lubricant film increases from 0.4 nm to 0.5 nm at the same baking time of 30 min with an increase of the applied lubricant film thickness from 4.7 nm to 12 nm. The bonded layer increases a little, from 0.5 nm to 0.6 nm, when the baking time increases from 30 min to 60 min at the applied lubricant film thickness of 12 nm.
Ellipsometry was used to measure the complex index of refraction (n-jk) of an unlubricated disk. The complex index consists of a real part (index of refraction) and an imaginary part (extinction coefficient). The index of the unlubricated disk was found to change from 1.462-j2.645 (before bake) to 1.502-j2.701 (after bake). The change in the index value was significant. It indicates that the chemical structure of the surface has been changed as a result of the baking of an unlubricated disk.
3.2. Effect of Sliding
The disks used for this part of the study were neither prebaked nor postbaked. Figure 2 shows the bonded lubricant film thickness as a function of sliding time. For Z-Dol, the bonded layer of lubricant film is higher after sliding in the case of a higher applied film thickness, that is, 36 nm versus 18 nm. The bonded fraction of the film remains at a low level and does not change significantly with the increase in sliding time for an applied film of 18 nm. For a 36-nm applied film thickness, the bonded fraction of the film increases significantly after the sliding time is increased from 0.5 h to 1 h. This indicates that if too thin a lubricant film is applied, it might be easily depleted. The consequence of this is reflected in the low bonded fraction. If the applied film is thick enough, then the increased sliding time enhances the bonding of lubricant to the surface.
TABLE 1. Chemical Structure and Selected Properties of PFPE Lubricants |
Lubricant | Formula | End Groups | Molecular Weight (Daltons) | Density (x10³ kg/m³ at 20°C) | Kinematic viscosity (mm²/s) |
Z-25 | CF3—O—(CF2—CF2—O)m—(CF2—O)n—CF3 | —CF3 | 1280 | 1.85 | 250 @ 20°C |
Z-15 | CF3—O—(CF2—CF2—O)m—(CF2—O)n—CF3 | —CF3 | 9100 | 1.84 | 150 @ 20°C |
Z-DOL¹ | HO—CH2—CF2—O—(CF2—CF2—O)m—(CF2—O)n—CF2—CH2—OH ; (m/n ~ (2/3) | —OH | 2000 | 1.81 | 80 @ 20°C 34 @ 40°C |
¹ — Functional or polar lubricants
|
TABLE 2. Effect of Prebaking at 150 °C for 2 h on the Bonded Film of Lubricant Z-DOL¹ |
Lubricant | Postbaking Time (min) | Disk B1 | Disk B2 |
Prebaking |
Yes | No |
Applied | 45 | 3.4 nm | 3.4 nm |
Bonded | 45 | 1.0 ±0.08 nm | 0.4 ±0.04 nm |
Applied | 30 | 4.7 nm | 4.7 nm |
Bonded | 30 | 0.8 ±0.06 nm | 0.4 ±0.05 nm |
Applied | 30 | 12 nm | 12 nm |
Bonded | 30 | 1.0±0.09 nm | 0.5 ±0.05 nm |
Applied | 60 | 12 nm | 12 nm |
Bonded | 60 | 1.2±0.09 nm | 0.6 ±0.04 nm |
¹ — After postbaking at 150 °C for various times and washing by solvent FC-72.
|
In the case of nonpolar lubricants Z-15 and Z-25, the bonded layer after sliding is relatively low compared to Z-Dol. The bonded layer of the lubricant film increases with an increase in sliding time and levels off after ~8 h.
3.3. Mechanisms
3.3.1. Effect of Prebake
In the DLC disk surface that is not prebaked (Fig. 3), it is clearly demonstrated that the adsorbed water molecules interact with both dangling bonds and functional groups of the DLC surface (Zhao et al.. 1999). Two types of interactions are considered. The first one relates to hydrogen bonding that reflects in the interaction of water atoms with oxygen and/or hydrogen atoms of the DLC surface functional groups (x). The second relates to the passivation of dangling bonds by the partially charged water hydrogen atoms that reflect in the water hydrogen atom interaction, with the DLC surface dangling bonds depicted by dots. These kinds of interactions depend on the humidity of the environment and lead to the DLC surface deactivation. After the DLC surface is lubricated with polar PFPE lubricant Z-Dol molecules, the deactivated surface cannot strongly adsorb Z-Dol molecules, as shown in Fig. 4. This is the reason that the bonded layer of lubricant film on the disk surface without prebake is lower (Table 2).
In the case of prebaked disk surface, water molecules are evaporated leaving the surface active sites (dangling bonds and functional groups). This leads to the activated DLC surface (Fig. 5). The previously mentioned change in the measured substrate index between the unbaked and baked disks (unlubricated) proves this hypothesis. Now Z-DoL molecules have unlimited access to the DLC dangling bonds. The molecules interacting with the dangling bonds can also interact with the surface functional groups, forming a strongly attracted lubricant film to the surface. This situation is presented schematically in Fig. (3. In reality, the lubricant molecules are rather extended on the surface. The vertical portion of the Z-Dol molecules depicted in Fig. 6 is applied to better illustrate this kind of bonding process.
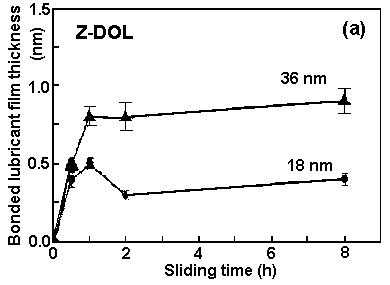 |
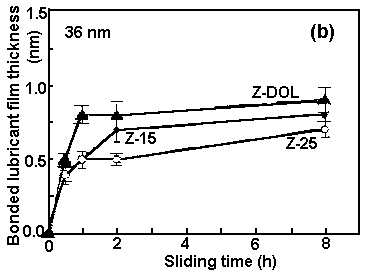 |
Fig. 2. Effect of sliding time on bonded lubricant film thickness for (a) Z-Dol and (b) Z-15, Z-25, and Z-Dol. The total lubricant film thicknesses on the disk surfaces are indicated.
|
• Dangling bond; — Covalent bond; « Hydrogen bond interaction; (x) Functional group
|
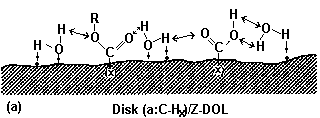 |
|
Fig. 3. Adsorption of water molecules on a DLC surface exposed to an ambient environment. R is an alkyl group, e.g., —CH3 group. |
Fig. 5. DLC surface after prebaking at 150 °C; water molecules are desorbed.
|
H |
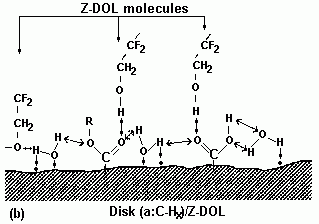 |
|
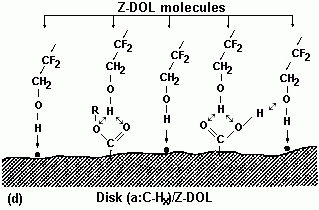 |
Fig. 4. Adsorption of Z-Dol molecules on a DLC surface exposed to an ambient environment. |
Fig. 6. Bonding of Z-DOL molecules on a DLC surface after postbaking at 150 ° C for 2 h.
| |
3.3.2. Effect of Sliding
To account for the sliding results, we hypothesize that one possible action mechanism for chemical bonding of PFPE lubricants with a DLC surface is connected with the formation of radical-anion reactive intermediates, caused by the reaction of low-energy electrons (exoelectrons) emitted during the sliding process. The energy of exoelectrons isconsidered to be very low, of the order of 2-3 eV (Chaikin, 1967).
Step 1 Low-energy electron emission process (1-4 eV) during sliding

Step 2 Attachment of emitted electron to lubricant molecule
Z-DOL + e → —CF2—CH2O¯ + H•
(Reactive species)
Step 3 Chemical reactions with the surface
Bonded molecule
H• species may recombine and generate hydrogen molecules H2
or they can interact with the dangling bonds
Bonded hydrogen atom
Fig. 7. Low-energy electron emission process during sliding on a Z-Dol lubricated surface and the interaction of emitted electrons with the lubricant molecules and subsequent interactions with surface. A simple dot represents the unpaired electron, known as a free radical. A free radical has no positive or negative charge but is very reactive because it is unpaired.
| | | | |
The approach is related to the negative-ion-radical concept of action mechanism of additives and hydrocarbons during sliding, reported by Kajdas (1985 a, b). The concept is based on the mechanism of ionization of these compounds, caused by the action of exoelectrons. Most recently Nakayama et al. (1997a,b) provided evidence that exoelectrons, apart from other charged particles, are emitted in a frictional system with diamond sliding on a:C-Hx films in ambient air. In this study, we relate the Z-Dol molecule ionization process as presented for alcohols (Kajdas, 1987); that is, the low-energy electron interaction with a —CH2OH group leads to the formation of a negative-ion-radical species [—CH2O]• — that decomposes to the negative ion —CH2O¯ and free radical H•. In the low-energy electron interaction process with nonpolar
PFPE lubricants Z-15 and Z-25, we relate to the work by Vurens et al. (1992), who demonstrated that the low-energy electron decomposition of PFPEs gives rise to a different set of products than thermal decomposition. Their data suggest that the electron decomposition occurs through the formation of a negative-ion resonance state. Then, as a result of C—O bond cleavage, a negative ion —CF2O¯ is formed and a reactive radical species (•CF2O¯) is generated.
Figure 7 shows the steps through which lubricant Z-Dol molecules are chemically bonded to the DLC surface after sliding. During the sliding, low-energy electrons are emitted at the interface (Step 1). These electrons then attach to lubricant molecules and form the reactive species —CF2—CH2—O¯ and H• (Step 2). The reactive group —CF2—CH2—O¯ can react with the surface and form bonded molecules —CF2—CH2—O— (Step 3). H• species may recombine and generate hydrogen molecules H2, or they can interact with dangling bonds on the surface.
Figure 8 shows the steps through which lubricant Z-15 or Z-25 molecules are chemically bonded to the DLC surface after sliding. Step 1 is similar to
Step 1 Low-energy electron emission process (1-4 eV) during sliding

Step 2 Attachment of emitted electron to lubricant molecule
—CF2—O—CF2— + e → —CF2—O¯ +•CF2—
Step 3 Further Chemical reactions a) with the surface
Bonded molecule
Bonded molecule
b) between lubricant fragments
•CF2— + •CF2— → —F2C—CF2—
Z15 + •CF2— → [Z-15—F]• + CF3—
| | | |
|
Fig. 8. Low-energy electron emission process during sliding on a Z-15 or Z-25 lubricated surface and the interaction of emitted electrons with the lubricant molecules and subsequent interactions with the surface.
|
that in Fig. 7. The low-energy electrons then attach to lubricant molecules and form the reactive species •CF2O¯ and •CF2O— (Step 2). The reactive group —CF2O¯ allows chemical reaction with the surface and forms bonded molecules —CF2—O— (Step 3). Radical species •CF2O— can react with the surface and form the dangling bond —CF2O— on the surface (Step 3). Free radicals •CF2O— can recombine, forming a PFPE molecule, or they can interact with Z-15 lubricant molecules, producing a smaller PFPE compound and generating another free radical [Z-15-F]•. The latter radical can recombine with a •CF2O— free radical, generating a higher molecular-weight lubricant compound.
4. conclusions
The chemical bonding of PFPE lubricants on a DLC surface can be enhanced by either prebake and/or sliding. For polar lubricants such as Z-Dol, prebake can activate the DLC surface and hence increases the access to lubricant molecules that can chemically bond on the surface. The prebaked DLC surface can increase the fraction of the bonded layer by a factor of 2. For polar and nonpolar PFPE lubricants including Z-Dol, Z-15, and Z-25, sliding at the interface can emit low-energy electrons. The electrons can attach to the lubricant molecules and allow the chemical reaction between lubricant molecules and a DLC surface. This enhances the chemical bonding.
ACKNOWLEDGMENTS
Financial support for this study was provided by the industrial membership of the Computer Microtribology and Contamination Laboratory (CMCL).
REFERENCES
- Bhushan, B. (1996), Tribology and Mechanics of Magnetic Storage Devices, 2nd ed., Springer-Verlag, New York.
- Chaikin, S. W. (1967), "On Frictional Polymer," Wear 10, 49-60.
- Kajdas, C. (1985a), "On Negative-Ion Concept of EP Action of Organo-Sulfur Compounds," ASLE Trans. 28, 21-30.
- Kajdas, C. (1985b), "About a Negative-Ion Concept of the Antiwear and Antiseizure Action of Hydrocarbons during Friction," Wear 101, 1-12.
- Kajdas, C. (1987), "About an Anionic-Radical Concept of the Lubrication Mechanism of Alcohols," Wear 116, 167-180.
- Nakayama, K., Yamanaka, K., Ikeda, H., and Sato, T. (1997a), "Friction, Wear, and Triboelectron Emission of Hvdrogenated Amorphous Carbon Films," Tribol. Trans. 40, 507-513.
- Nakayama, K., Bousaid, B.. and Ikeda, H. (1997b), "TriboElectromagnetic Phenomena ofHydrogenated Carbon Films-TriboElectrons," ASME J. Tribol. 119, 764-768.
- Vurens, G. H., Gudeman, C. S., Lin, L. J., and Foster, J. S. (1992), "Mechanism of Ultraviolet and Electron Bonding of Perfluoropolyethers," Langmuir, 8, 1165-1169.
- Zhao, Z., and Bhushan, B. (1996), "Effect of Bonded Lubricant Films on the Tribological Performance of Magnetic Thin-Film Rigid Disks," Wear 202, 50-59.
- Zhao, Z., Bhushan, B., and Kajdas, C. (1999). "Tribological Performance of PFPE and X-1P Lubricants at Head-Disk Interface. Part II. Mechanisms," Tribol. Lett. 6, 141-148.
|