|
Major Pathways for Used Oil Disposal and Recycling. Part 1
Czeslaw Kajdas
Warsaw University of Technology, Institute of Chemistry in Plock and Central Petroleum Laboratory in Warsaw, Poland
Abstract
One of the main concerns with lubricating oil relates to used oil management/or both industrial and engine oils, although the environmental impact of gasoline and diesel engine oils is the most critical. Provided that efficient management systems are in place, most used oil should not reach the environment, so, the major question is how to dispose of collected used oil.The first option lies in burning it as a fuel, the second in recycling (reclaiming, reprocessing, re-refining). The latter allows recovery of mineral base oils, which are valuable constituents of crude oil.
Mobile (on site) and fixed plants for industrial oil recycling will first be discussed, and the paper will look at the most modern re-refining processes that produce base oils of as high quality as virgin base oils. Based on current re-refining experience, the quality of finished lubricants blended from re-refined base stocks is also noted. Re-refining today may be of significant benefit to the economy and can, of course, protect the environment. All modern re-refining technologies produce small amounts of by-products in which toxic materials may have been concentrated. A final aspect of reprocessing used oil is to integrate it, after hydrogen treatment, into existing refineries. Tilis valuable raw material can then be directly routed to a lube oil unit or even to a cracking unit for conversion to gasoline. The integration of used oil treatment processes into selected refineries may be t1ic most effective pathway to used oil disposal.
In this first part, the author looks at the nature of the problems associated with used oil, its use as a fuel, and simple recycling. He then goes on to look at major rerefining processes, starting with hydrogenation (KTl, Mohawk, BERC/NIPER, and PROP technologies). Part 1 will describe oilier processes, including a range of vacuum distillation/clay treatment technologies.
Keywords
used oil, disposal, recycling, burning, hydrogenation, KTl, Moliawk, BERC, NIPER, PROP
* Published in: Tribotest journal 7-7, September 2000. (7) 61
INTRODUCTION
Waste may be defined as any material rejected as unfit for further use. There are many wastes hazardous to mankind, including used oils, especially those contaminated with polychlorinated biphenyls (PCBs), heavy metals, or carcinogenic polycyclic aromatic hydrocarbons (PAHs). It has been widely acknowledged that the environmental consequences of our lack of attention to pollution control over the past century has brought about polluted air, drinking water, and soil in many countries. This has now also spread to developing countries. One widespread hazardous waste is used lubricating oil. A measure of used oil's threat to the environment can be demonstrated by the fact that only one litre of used oil is enough to pollute a million litres of fresh water, i.e., one part of oil per one million parts of water can cause taste and odour problems in drinking water. Concentration of some 30 to 40 ppm of used oil in water produces a visible oil slick that can damage aquatic life, and 50 ppm can foul a waste water treatment process. This can be much more dangerous where the oil contains compounds toxic to humans, such as PCBs, which generate dioxins. Disposal of used oil to land was a widely accepted practice until some unfortunate consequences became apparent, as at Times Beach in the USA, where the town had to be abandoned as a result of dioxin-adulterated waste crankcase oil being sprayed on roads to control dust.1
Disposal of used oil as a hazardous waste requires it be incinerated at a temperature exceeding 1200°C to ensure complete oxidation of PCBs, polychlorinated terphenyls (PCTs), and PAHs. Such disposal is mandatory in many countries if the amounts of certain contaminants in the used oil exceed predetermined levels. Recently the Council of the European Union (EU) adopted a revised Directive setting deadlines for the disposal of PCBs and PCTs in EU Member States; this replaced the 1976 Directive which had 'become obsolete since the ban on the sale of these compounds and the progress made in techniques for their disposal'. The Directive wants most remaining PCBs requiring disposal in Europe to be accounted for, and to harmonise legislation on their disposal across EU Member States. The Directive does not apply to materials with a PCB concentration of < 50 ppm, which relates to the fact that in many countries used oils with >20Dpm PCBs must be incinerated at a temperature of > 1200°C. Another Directive² requires that: 'used oils are to be collected and disposed of without causing any avoidable damage to man and environment'.
Used oil generation and collection: What is 'used' oil?
Used oil generation is strictly related to lubricating oil consumption. On average, -50% of lube oil consumed can be regenerated for reuse. Automotive
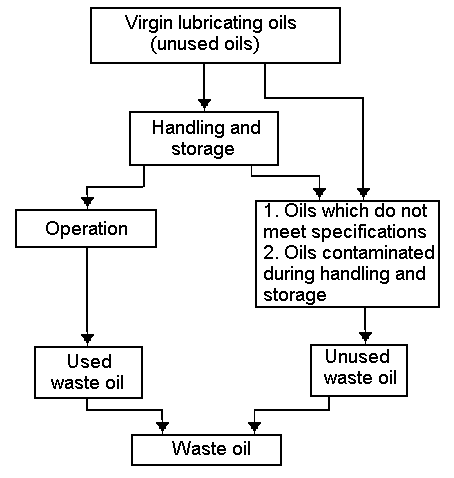 |
Figure 1 Generation of used (waste) oil
|
gasoline and diesel engine oils, together with railroad diesel engine oils, are the major lubricant products. Most of them are mono- and multigrade crankcase lubricants, along with gear lubricants and transmission fluids. There are several potential sources of used motor oils, including service stations, do-it-yourself (DIY) motorists, company fleets, and specialised used oil collection points.
Used oils are usually significantly contaminated. Besides normal degradation compounds/products, a wide range of contaminants can be encountered, including:
- residual components of engine fuels (gasoline and diesel fuel);
- solids from wear processes and additives, along with corrosion products and dirt;
- soot;
- combustion products (water, acids);
- various chemicals.
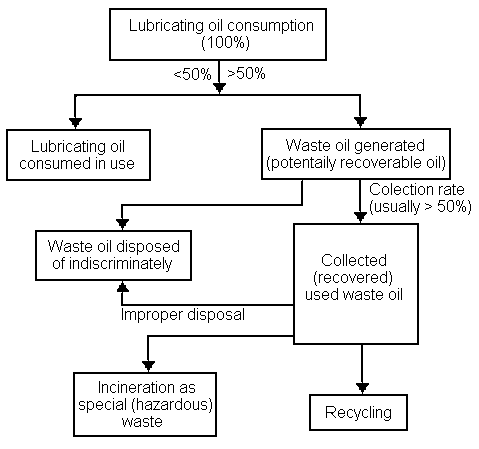 |
Figure 2 Used oil generation and collection
|
Figure 1 is a scheme representing the generation of waste oil. The terms used here, defined according to reference 3, include:
Used waste oil A mineral or synthetic lubricating oil whose physical and chemical properties have changed in use such that it is not fit for its original purpose.
Unused waste oil Unused virgin oil that has become contaminated when spilled or mixed with other waste, or that has failed to meet specifications.
Waste oil Oil which has become contaminated during storage, handling, or use. It is made up of both used and unused waste oils.
Figure 2 provides an indication of the paths to the generation and collection of used waste oil. By and large, the availability of used waste oil relates directly to lubricating oil usage. The greater the usage, the larger the quantity of potentially recoverable waste oil for reutilisation, which amount equals the fraction available for collection in the waste oil management system, and does not include the oil in waste water treatment sludge at industrial sites.
The ideal would be to collect all the used oil generated. However, this is not an easy task. In the EU, a volume of some 5 million tons of lubricating oils is consumed yearly, the used oil generated by this being around 50%, i.e, 2.5 million tons. Of this, only about 60%, or 1.5 million tons, is collected, so approximately 1 million tons remain unaccounted for. A general overview of the collection and disposal of used oils in Europe is described in reference 4.
Collection is mostly financed either through a tax on both new and regenerated lubricating oils or through a contribution from used oil generators. Educational efforts should raise awareness of the damage used oil can inflict if disposed of improperly. Usually, the collection system works best when carried out by licensed independent collectors in a specific area. Also important are procedures, for example, to encourage DIYers to reuse their used oil containers. Promoting any used oil recycling programme should include: (1) advice on how to manage collected used oil properly, (2) information about the importance of collecting used oil, (3) explanation of how to take advantage of a given programme. Specific measures may also help: in Japan, for example, the public is required to turn in their used oil in order to buy new.
Disposal and recycling
Used oil disposal refers to non-reuse of the oil. Disposal options here include dumping on landfill, landfarming, dust suppression, incineration, and any indiscriminate dumping. Recycling of used oil relates to passing it through a cycle of changes or treatment which provides products or materials for reuse, and usually employs one or more of the three methods for commercial regeneration of used oils: reclaiming (or reconditioning), reprocessing, or re-refining.
Reclaiming and reprocessing are done in many countries, mostly in inplant recycling. Depletion of crude oil reserves and increased concern for the environment are stimulating factors contributing to increased re-refining of waste automotive oils, which account for over 50% of all waste oil. Figure 3 presents a general scheme of waste oil recycling. The terms used are as follows:
Reclaiming or reconditioning is the processing that mostly removes solids and water by simple physical methods (settling, heating, filtration, centrifuging) but does not remove unwanted oil-soluble contaminants.
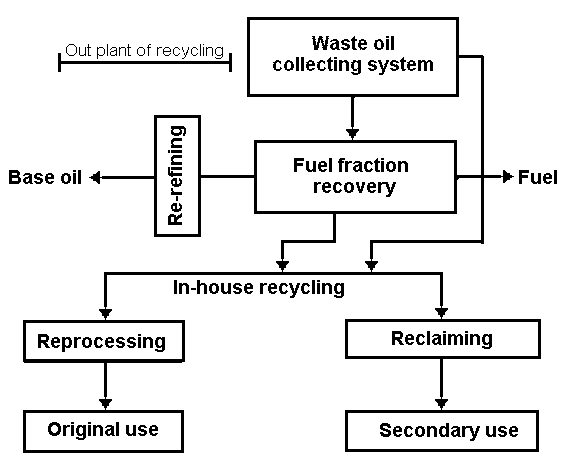 |
Figure 3 Used (waste) oil recycling
|
Reprocessing removes solids, water, and some soluble contaminants using chemicals. Use of adsorbents may also be part of reprocessing. Reprocessing also relates to fuel oil production from waste oil with mild cleaning.
Recycling of waste oil can therefore be accomplished in several ways. The first is in-house recycling, within the user facility, and hence potentially the most efficient; in many cases the lubricant removed from the lubrication system is contaminated, but not seriously degraded. In other words, the base oil and additives are almost unchanged after use, but the amount of water, dirt, or wear debris is so great that the oil is no longer fit for use.
The economic importance of used oil recycling can clearly be seen in the following example:5 Alabama generates 17 million gallons of used automotive oil annually (approximately 25% of this used oil is generated by do-it-yourself engine oil changers). If this were recycled it would provide the energy necessary to power 50,000 automobiles for one year.
Indiscriminately disposed-of used oil pollutes the environment and thereby poses a threat to public health. Dumping of used oil and/or disposal, such as road oiling to suppress dust, or use as a wood preservative, can threaten the environment by drainage into the water table, threatening aquatic life and drinking water. Uncontrolled burning of used oils can significantly pollute, while the use of used oils in bitumens is also dangerous as bitumens are commonly applied at high temperatures, with the potential for the release of toxic fumes. One of the main concerns relates to the quality of management of both industrial and engine oils. A well-managed used oil collection system can minimise both the variability of the material supplied to a recycling plant, and the problem of contamination by toxic or hazardous materials, for instance, polychlorinated biphenyls.
With efficient management systems, most used oil should not reach the environment, although two-stroke oils are simply lost during their application. Thus, the major question is how to dispose of used oil that had been collected. The first option is burning it as a fuel, the second is recycling (reclaiming, reprocessing, or re-refining).
UNIDO studied the disposal of waste oil in twelve developing countries, and organised workshops, with delegates from 35 countries. Their major conclusions were that the safest disposal route for waste oil was to re-refine it, to recover the base oil,6 used oil being a valuable resource that should be recycled. It has been suggested6 that, with appropriate government support, re-refining could be financially viable, with minimal environmental and health risks. Industrial used oils in particular can yield a high quantity of regenerated base oil.
This paper will discuss the most recent re-refining processes, which can produce base oils as good as virgin base oils. Mineral base oils are the most valuable constituents of crude oil, although an average crude oil contains only 5-15% base oil, whereas used automotive oils contain 70-75% base oil; the latter should thus be treated as a valuable resource.
Current re-refining technologies incorporate a vacuum distillation process that concentrates most of the contaminants in the vacuum residue, and produces the required viscosity in the re-refined base oil fractions. Other steps may include chemical pretreatment, solvent extraction, wiped-film evaporation, hydrotreatment, and clay polishing. A good review of acid/clay treating processes is given in reference 7.
USED OIL AS FUEL
The most common use of waste oil products is as a fuel for industrial furnaces that would otherwise use more expensive fuel oil. However, this represents a significant threat to the environment as pretreatment is usually limited to simple filtration to remove solid contaminants. Accordingly, all the contaminants remain in the fuel oil and, as a result of the relatively low combustion temperature, most toxic components will reach the environment with the flue gas. In some cases, the contaminants may damage the furnace or its components, leading to increased pollution. The combustion conditions in most cement kilns are such as to allow safe disposal of toxic contaminants in the used oil, provided the kiln has a suitable exhaust gas cleaning system. The safe incineration of PCBs at 1200°C needs a minimum residence time of 4 s. Burning under controlled conditions may be the only option where used oil is generated in small quantities over a large geographical area.
To mitigate environmental damage, mainly by heavy metals and halogens, specific regulations have been established, e.g., the US government 1990 regulations8 governing collection, transportation, testing, and ultimate use of waste oil, which mandate testing by certified laboratories to establish levels of arsenic, cadmium, chromium, lead, and halogens.
Where used oil is used as a blending component for residual fuel oil, minimum pretreatment should include settling to separate water, and heat treatment to remove the remaining water and light ends (volatile components resulting from any engine fuel or solvents present). Quality checks should be made for toxic components, particularly PCBs.
Combustion of used oil as burner fuel is condemned because it destroys a valuable resource, and can cause substantial pollution through the dispersion of metal oxides and stable organic contaminants. On the other hand, under certain conditions, and with adequate precautions, the use of used oil to produce heat can be a valid pathway.
SIMPLE RECYCLING
Used oil can be recycled (reclaimed) within the user facility, or be sent to a commercial reclaimer. The primary difference between these two options is usually the level of treatment available: in-plant reclaiming is generally limited to gravity purification or settling, filtration, centrifuging, and heating to remove volatiles and water, and can in many cases purify certain used oils enough to meet heating fuel requirements. A commercial reclaimer can normally perform all of the above, plus demulsification, chemical treatment, distillation, clay treatment, and reformulation with additives. It is important that the oil is segregated at source, as a mixture of high and low quality oil can be reclaimed only as a low quality oil product or simply as a fuel. The product of a reclaiming procedure is a lubricating oil, which can meet original specifications, for uses such as hydraulic oils, gear lubricants, and metalworking fluids (metal rolling lubricants, cutting oils, grinding fluids).
A good example of simple mobile used oil recycling are the CHEM-ECOL process units,9 which are trailers, or trucks, and which are becoming larger and more sophisticated. Thus, one of the latest units processes low-viscosity oils at rates in excess of 3,000 US gall. per hour, can process high-viscosity gear oils (e.g., ISO 680) at rates of over 1,500 gall. per hour, and can handle emulsifier water at levels of 10% or more. The unit is completely self-contained, with a propane heating system and a 50 kW diesel generator for phase power; computers control the speed of operation, and check for water content and filter problems, although this can also be run manually. The unit will filter to 0.45 µm and provide ISO particle counts. Normal filtration levels are to micron nominal, and residual water levels are typically below 50 ppm. Additives that bring the levels back to new oil concentrations, can be blended in with continuous metering pumps during the process. CHEM-ECOL also does fixed installations that process volumes as large as truckloads.
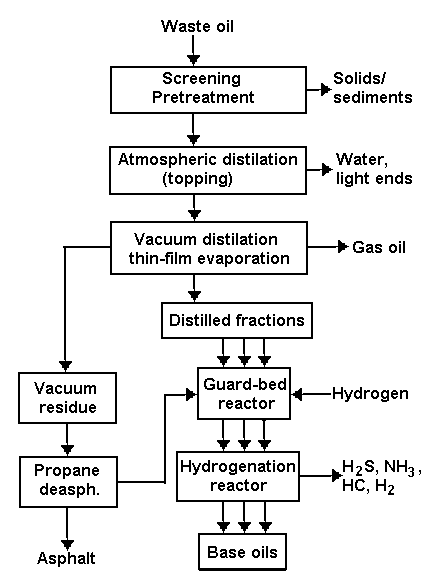 |
Figure 4 Vacuum distilation / hydrogenation processing of used oils
|
Another example of used oil recycling is given by Smallman Lubricants Ltd., UK, who, since 1974, have provided an oil recycling facility for the oils they provide, so giving an integrated supply and recycling service. The advantages are quality assurance, process efficiency, reduced transport costs, and flexibility10, and the service covers a wide range of industrial products.
MAJOR RE-REFINING
The purpose of re-refining is to produce clean, high-quality base oils. This may include pretreatment to reduce the impurity content, vacuum distillation, and other divers stages such as solvent extraction, thin-film evaporation, or hydrogenation to yield base oils as good as the original.
Modern lubricating oils, particularly multigrade engine oils, have rendered conventional acid/clay based technologies insufficient to return used oil to its original quality with a satisfactory yield. In addition, environmental pressures are making it more difficult to dispose of the processing wastes. To overcome these problems, vacuum distillation and hydrogenation have been widely introduced.
Such processes involve distillation of dehydrated waste oil in a thin-film evaporator, and subsequent hydrotreating of distilled stocks. Figure 4 presents the essential steps of this technology. Water and low-boiling hydrocarbons are first removed ('topping'). The feedstock contains both the recoverable base oil fractions and a mixture of high-boiling materials which can be removed as a bottom product. Distillation is carried out either in a conventional vacuum column similar to that for the production of raw lubricating oil distillates, if the oil is not too dirty, or in a high-vacuum wiped-film evaporator. The latter works by introducing liquid at the top of a tall cylinder with a heated jacket. The waste oil flows uniformly down the inside of the column while a rotating blade wipes the surface to ensure a thin film. This secures good heat transfer and a large surface for evaporation with minimum heating time, to reduce cracking.
Wiped-film distillation can be carried out in several ways: multiple evaporators can be sequenced to provide several lubricating oil fractions, or a single unit can be used for single or multiple passes. In the latter case the bottoms from the previous run become the feedstock for the next higher boiling temperature
fraction. One prime attraction of wiped-film vacuum distillation is that it can be retrofitted into older facilities. The preliminary and finishing steps are the same as used in most refineries. An additional attraction is the absence of a pretreatment step to prevent the coking and fouling that occur in normal vacuum distillation columns.
Hydrofinishing stabilises the undesirable compounds by mild hydrogenation. Oxygen-containing compounds, for example, are converted into lower boiling hydrocarbons and water. Similarly, sulphur and nitrogen compounds react to form hydrogen sulphide and ammonia. Usually, hydrofinishing removes all of the oxygen-containing compounds and 50% or more of the sulphur, but only very little of the nitrogen. Mild hydrotreating removes most of the nitrogen compounds, which appear to be largely responsible for poor colour and colour stability. Severe hydrotreating induces extensive hydrocracking in addition to saturation of aromatics and destructive hydrogenation of non-hydrocarbons. The residue is mostly used as a bitumen material. Alternatively, by using propane deasphalting, bright stock can be recovered. With propane extraction/distillation (the Interline process) the obtained residuum can be used as an asphalt modifier.
At present around 35% of the used oil collected in Europe is re-refined to base oils, although throughput is only some 70% of the maximum possible. Processes range from acid/clay re-refining to more complex distillation (e.g., wiped-film distillation, Viscolube distillation) and are continually under development. Re-refiners include Viscolube Italiana, IFF, Re-refinery Dollbergen, and DEA Hamburg. Some collaborative projects exist, aimed at improving re-refining processes. In the USA and Canada the market for used oil is significant, and re-refining is playing a role that is growing with new technologies.
Hydrogenation - KTI
The KTI (Kinetics Technology International) process, also known as KTI Relub Technology, combines vacuum distillation and hydrofinishing to remove most of the contaminants from the waste oil. The basic stages of this process comprise: atmospheric and vacuum distillation, hydrofinishing of the vacuum distillates, and fractionation. In this technology, an atmospheric distillation column removes water and light hydrocarbon fractions, while a first vacuum unit produces a product in the lubricating oil range. This process has no pretreatment step, because it uses a special vacuum distillation that minimises thermal stress by applying temperatures not in excess of 250°C in short bursts11. These conditions favour thin-film evaporation. By using a wiped-film evaporator, the facility can take most types of feedstock.
The distilled oil is then mixed with hydrogen, heated and passed through a reactor to remove sulphur-, oxygen- and nitrogen-containing compounds and improve the colour. The hydrogenated oil is finally stripped with steam or fractionated into different base oil fractions depending upon the product requirements and specifications. This technology accepts PCBs and other hazardous materials, and produces high-quality base oils with a yield of about 82%. Polluting by-products are minimised. The vacuum residue generated contains additives, asphaltenes, oxidation/polymerisation products, metal and other impurities. The residue has commercial value. At the present time, several plants are in commercial operation. KTI completed its first industrial plant in Greece in 1982.
Hydrogenation - Mohawk
This technology was developed by the Mohawk Oil Company of Vancouver, Canada, and is based on the KTI process. A disadvantage of hydrofinishing over clay contacting is the higher investment cost. On the other hand, the advantages of hydrogen include improved base oil yields and quality, and freedom from waste disposal problems. Hydrotreating of distilled lubricating oil cuts can be conducted in two reactors in series, as shown in Figure 4. The first reactor contains a guard-bed material with a high surface area (usually alumina) and the second contains a hydrotreating catalyst. The alumina removes any metal contaminants, for example, zinc or lead, that may have remained in the waste oil after distillation. Even a low parts-per-million level of these contaminants is detrimental to the hydrotreating catalysts.
Usually, the optimum temperature for guard-bed reactor operation is in the range 290-300°C. Temperatures above 310°C produce dark coloured residues that degrade product colour, while temperatures below 275°C reduce metal removal drastically. The optimum temperature for the hydrotreating reactor seems to be approximately 50°C higher than for the guard-bed reactor. Increasing reactor temperature usually improves product colour and clarity. Operating at temperatures above 350°C improves product colour and reduces the sulphur, nitrogen, and halogen content, but increases total hydrogen consumption. Process pressure does not significantly affect product quality, although the nitrogen content decreases with an increase in hydrogen pressure. The main problem in the hydrotreating step is rapid catalyst deactivation. The proprietary feature of the Mohawk technology that distinguishes it from other vacuum distillation/hydrogenation approaches is understanding of the chemistry of the lubricating oil additives found in the waste oil under the influence of time and temperature. This understanding has led to processing techniques and operating conditions that provide superior performance in terms of onstream time, catalyst life, and corrosion resistance.
The essential steps of the Mohawk technology include: (1) proprietary pretreatment, (2) atmospheric distillation, (3) vacuum distillation, (4) wiped-film distillation, (5) hydrofinishing, and (6) fractionation.
The chemical pretreatment unit precipitates any contaminants present in the used oil, so eliminating fouling problems during distillation, and extending catalyst life. Atmospheric distillation removes water and gasoline. Vacuum distillation is used for recovery of lubricating oil hydrocarbons. Finally, hydrofinishing purifies the oil which is then fractionated to the base stocks required.
It is claimed that the Mohawk technology is the most advanced hydrogen based re-refining process, superior to similar processes, because it allows the plant to be run without frequent cleaning. The absence of fouling also permits a vacuum to be generated by mechanical means instead of steam jets, markedly reducing the amount of water that must be treated as effluent from the process. Cheaper construction materials can be used because of the absence of corrosion. The Mohawk technology has been licensed to Evergreen Oil in Newark, California, and Breslube in Windsor, Canada.
Hydrogenation - BERC/NIPER
Bartlesville Energy Research Center (BERC), now called the National Institute of Petroleum and Energy Research (NIPER), technology was developed by scientists of the US Department of Energy. The technology is similar to KTI, with the addition of a solvent treatment. Its essential steps include: (1) atmospheric distillation, (2) vacuum distillation, (3) solvent pretreatment, (4) solvent recovery, and (5) fractional distillation followed by (6) either hydrofinishing or clay treatment. The incoming feed is first dehydrated at atmospheric pressure and stripped of light hydrocarbons in the vacuum column. After distillation, the product is then extracted with a 3:1 mixed solvent, composed of butyl alcohol, isopropyi alcohol, and methyl ethyl ketone (1:2:1). The solvent extraction removes coking and fouling precursors. The solvent waste oil mixture is allowed to settle, and sludge, including additives, heavy metals, and other dirt, is drawn off the bottom of the settling tanks or centrifuged to recover the oil and solvent. The solvent is recovered for reuse. The extracted oil is fractionated in a vacuum, followed by hydrogenation or clay treatment of base oil fractions to improve odour and to remove colour.
Hydrogenation - PROP
The PROP technology, developed by the Phillips Petroleum Company, combines chemical demetallisation and hydrogenation to remove contaminants from the waste oil. The process begins by mixing an aqueous solution of diammonium phosphate with heated waste oil to reduce the metal content of the oil. Chemical reactions lead to formation of metallic phosphates, which are subsequently removed by filtration. The remaining oil is then flashed to remove light hydrocarbons, gasoline, and water. Next, the oil is mixed with hydrogen and percolated through a bed of clay, and passed over an Ni/Mo catalyst in the hydrogenation reactor. The adsorption step removes the remaining traces of compounds which might poison the catalyst. During the hydrogenation process, sulphur-, oxygen-, chlorine-, and nitrogen-containing compounds are removed and the oil's colour is thereby improved.
The major solid by-product is described as neutral phosphate material with no potential disposal problem. For example, this by-product can be safely disposed of in a landfill. Liquid stream by-products relate to light ends and heavy gasoline which can be used as fuel. However, the used catalyst is typically to be treated as a hazardous waste.
In Part 2, the Safety Kleen process, IFP/SNAMPROGETTI, UOP DCH (Hylube), a range of vacuum distillation/clay treatment technologies, and some other processes will be examined.
References
- Cough, M., Dioxin Agent Orange: The Facts, Plenum Press, New York, 1986. ch. 7.
- EU Directive 87/101.
- Mueller Associates/ Inc., Waste Oil Reclaiming Technology, Utilization and Disposal, Noyes Data Corporation, Park Ridge, N), 1989.
- De Winter, D., 'Collection and disposal of used oil in Europe', in Proc. 3rd Eur. Congr. Re-refining, Lyon, France, 1996.
- April, C.C., and Powell, S.U., 'Project ROSE - Alabama's used oil recycling program', Waste Managment, 14 (1994)237-41.
- Puerto-Ferre, E., and Kajdas, C., 'Clean technology for recycling waste lubricating oils', in Proc. 9th Int. Coll. Trib., 'Ecological and Economical Aspects of Tribology', Technische Akademie Esslingen, Germany, January 1994, vol. 2, pp. 13.9/1-13.9/10.
- Dang, C.S., 'Re-refining of used oils - a review of commercial processes', Tribotest, 3, 4 (1997) 445-57.
- 'Hazardous waste bunker for energy recovery', 40 CFR, Part 266 Subpart D, Code of Federal Regulations, July 1,1990.
- 'Mobile and fixed plant recycling', CHEM-EC01. Ltd., January 1996, Ontario, Canada.
- Neadle, D.J., 'Lubricants recycling', in Proc. 9th Int. Coll. Trib., loc. cit., pp. 13.8/1-13.8/3.
- Oosterkamp, P.V.D., 'KT1 re-refining technology', paper presented at UNlDO-sponsored workshop, Karachi, Pakistan, 1992.
A revised version of a paper first presented at the 11th International Colloquium on Tribology, Technische Akademie Esslingen, Ostfildern, Germany.
|